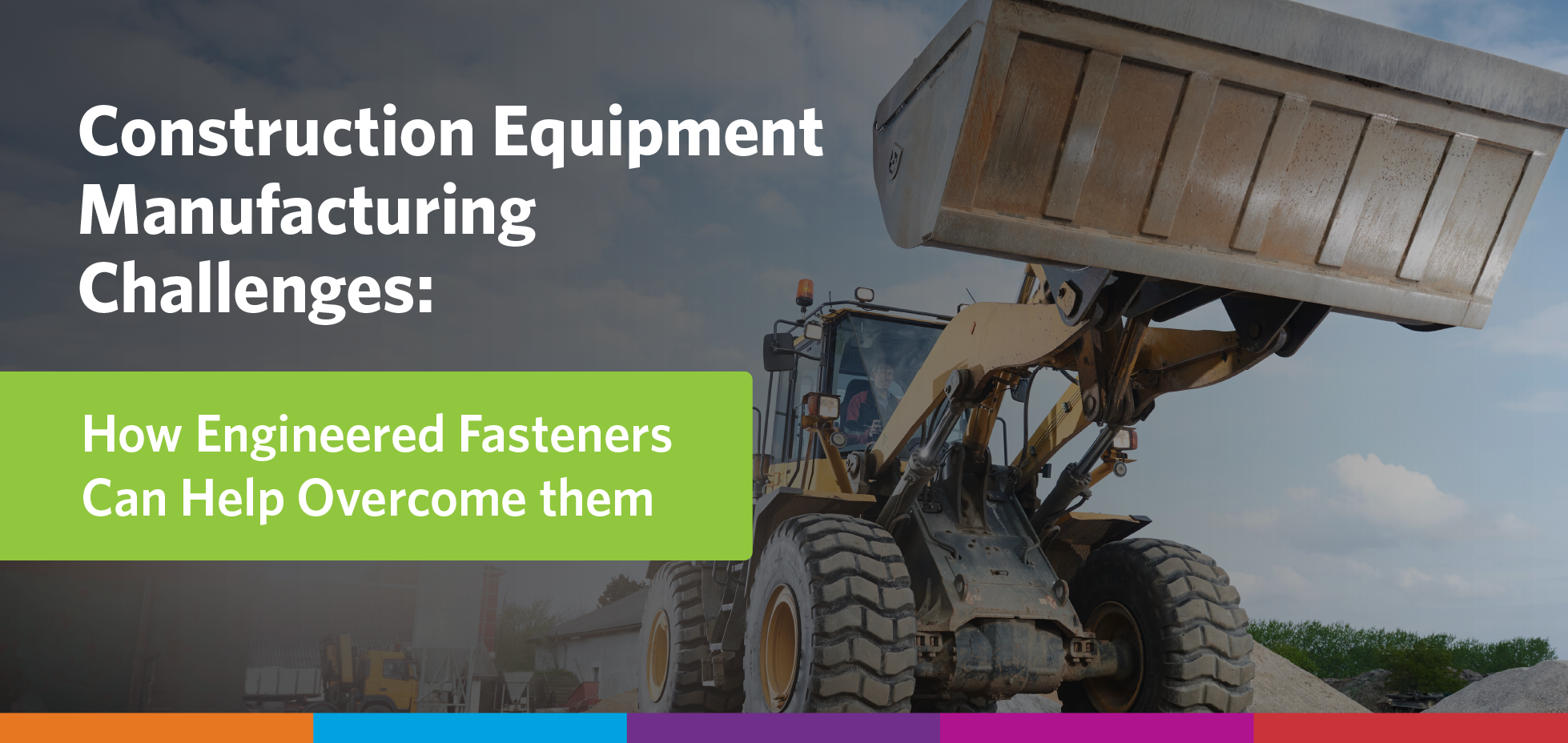
Overcoming Common Challenges in Construction Equipment Manufacturing: How Engineered Fasteners Can Help
The off-highway construction equipment manufacturing sector faces many challenges as it adapts to evolving technologies and market demands. Among these challenges are durabilité, electrification, supply chain resilience, durability, and customer expectations. Surprisingly, one of the most effective solutions to these issues lies in the seemingly simple realm of attaches techniques. Far from simple nuts and bolts, engineered fasteners provide critical enhancements to construction equipment. Manufacturers and distributors like Optimas are stepping up, offering innovative fastening solutions that support technological advancements, improve performance and enhance production efficiency. Here’s five ways engineered fasteners can address the specific challenges faced by the industry today.
Sustainability and Emissions Reduction
Challenges: As the industry pivots toward electrification and sustainability, manufacturers are under pressure to minimize environmental impacts through improved equipment design and eco-conscious supply chains. Key issues include battery life, charging infrastructure, and lifecycle management.
Solutions:
- Lightweight Engineering: Using engineered fasteners made from lightweight, high-strength materials, such as titanium aluminum alloys, help cut down on equipment weight, boost energy efficiency and meet strict emissions standards.
- Recyclable Fasteners: Fasteners designed for easy removal and recycling support manufacturers’ sustainability goals, enabling a shift toward circular economy models that prioritize repair, recycling, and reduce waste.
Electrification and Autonomous Equipment
Challenges: Integrating telematics, sensors and IoT is essential for enabling predictive maintenance, real-time monitoring and efficient fleet management. Additionally, the rise of autonomous construction equipment, including self-driving haulers and excavators, presents new opportunities and challenges. Manufacturers must focus on developing newer models and providing easy-to-implement add-on technologies for existing product lines to stay competitive in this evolving landscape.
Solutions:
- Custom Fasteners for Electric Systems: Specialized fasteners are needed to withstand the unique demands of electrified components, ensuring they endure heat, vibrations, and electromagnetic interference while maintaining safety.
- Quick Assembly and Maintenance: Fasteners that enable rapid assembly and disassembly minimize downtime on a project site for autonomous equipment. They also allow for easy adaptation of equipment to different configurations, reducing complexity in design and assembly while enhancing the equipment’s versatility.
Supply Chain Resilience
Challenges: Manufacturers are rethinking supply chain strategies in response to disruptions, inventory shortages, and variations in raw material costs.
Solutions:
- Local Sourcing and Agility: Fastener manufacturers with regionalized distribution networks can provide localized production and rapid delivery options, mitigating supply chain disruptions and minimizing production delays.
- Component Standardization: Standardizing fasteners across different equipment models can reduce the number of SKUs needed, streamlining the supply chain, minimizing inventory costs, and contributing to lean manufacturing processes, increasing productivity on the assembly line.
Durability and Performance in Harsh Environments
Challenges: Off-highway equipment operates in rough conditions, requiring robust components that can withstand exposure to weather, vegetation, mud, moisture, and chemicals.
Solutions:
- Corrosion-Resistant Fasteners: Utilizing fasteners made from corrosion-resistant materials and advanced coatings can significantly enhance the longevity and performance of construction equipment.
- High-Stress Applications: Fasteners designed to handle high-stress situations improve the reliability and safety of critical systems, such as hydraulics and drivetrains.
- Vibration-Resistant Fasteners: Fasteners that mitigate vibration—especially important in electric and hybrid equipment—can reduce the need for repairs.
Customer Expectations and Cost Efficiency
Challenges: Customers demand efficient, versatile machines that adapt to various job requirements, pushing manufacturers to balance customization with demand, usage and cost control.
Solutions:
- Engineered Solutions: Working closely with a full-service fastener provider, OEMs can design fasteners, to meet specific equipment, environmental and demand requirements, while enhancing performance, versatility and cost parameters.
- Cost-Effective Material Solutions: Fasteners that utilize cost-effective, yet high-performing materials help reduce overall production costs without sacrificing quality.
Conclusion
Engineered fasteners are a strategic asset for construction equipment manufacturers, offering solutions that tackle the industry’s toughest challenges—sustainability, resilience, and adaptability. As manufacturers embrace new builds, Optimas stands ready to deliver fastener solutions that improve performance, drive innovation, and support a sustainable future. For your next project, don’t overlook the role of fasteners. Partner with Optimas to maximize equipment efficiency and align with the industry’s evolving demands.