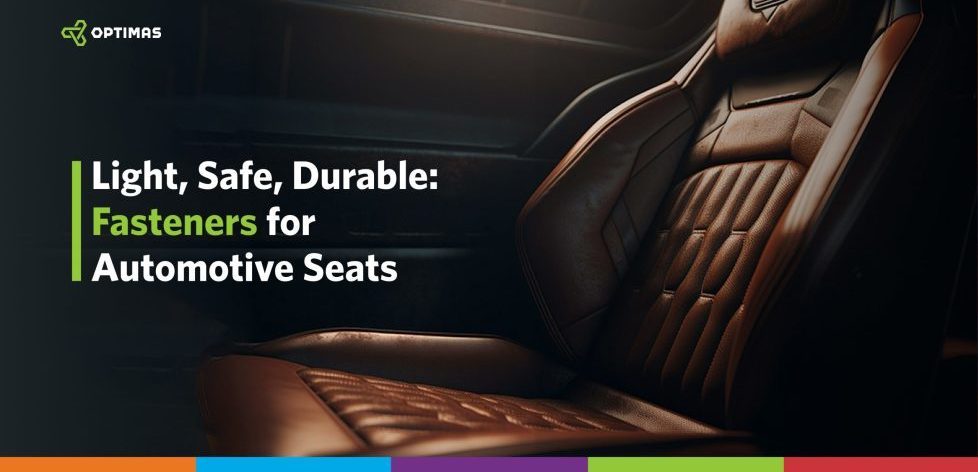
Light, Safe, Durable: Fasteners for Automotive Seats
According to the SMMT, over 775,014 cars and 101,600 commercial vehicles were built in the UK last year. Commensurate to this rise in production, seating manufacturers are experiencing heightened demand.
A significant portion of these newly manufactured vehicles are electric, and the era of electric battery technology has brought with it challenging technological demands for automotive OEMs. Lightweighting is a crucial consideration in all aspects of an EV build, as a 10% reduction in vehicle weight can result in a 6-8% improvement in fuel economy. All aspects of an EV, including seating, are expected to add minimal weight to the car.
Although they’re some of the smallest parts in a build, redesigning the geometry of a fastener can play a significant part in reducing overall vehicle weight. Re-engineering these parts can therefore considerably improve a seat’s suitability to an electric vehicle application.
Alongside this, the rapidly growing popularity of advanced climate-controlled seating, like chilling and heating seats, means that seat manufacturers are turning to increasingly advanced fastening solutions. Of course, vehicle safety and driver comfort also remain at high priority, leaving manufacturers with a number of key design considerations to satisfy.
Engineering Support
To satisfy these technological demands, seating manufacturers must use fasteners and components that are:
- Lightweight
- Vibration resistant
- Prioritise thermal and electrical conductivity and insulation
- Durable, with high tensile strength
Alongside manufacturing and distributing a range of standard and specialised fasteners and components, our in-house design engineers offer bespoke support for seating manufacturers.
With decades of experience working within the automotive industry, our engineers can work with you on a project basis or on-site to support you in product development, assembly and testing.
Offering 3D-printing and bar-turning capabilities, we also offer rapid prototyping for our partners, making sure to find the optimum fit for any seating application. Optimas is also a Global Centre of Excellence, specialising in rapid approvals for PPAPs (Production Part Approval Processes), minimising manufacturers’ time to market.
Alongside catering for more specialised applications, we provide a wide range of standard fasteners for automotive seats, including but not limited to:
- Weld Nuts
- SEMs Screws
- Machine Screws
- Flat Washers
- Rivet Nuts
- Plastic Parts
- Headed Pins
- Flanged Fasteners
Supply Chain Solutions – Onshoring and Nearshoring
While part optimisation is crucial, making sure these parts are received at the right place, at the right time is essential to meet demand.
Supply chains are forecasted to remain in a state of unpredictability, so it’s important manufacturers streamline their supply chains. Plus, with the evolving strictness of the UK’s ‘Rule of Origin’ legislation, many UK manufacturers are looking to onshore their fastener supply to qualify for the benefits of any EU-UK trade deal.
With a fastener manufacturing facility in Droitwich and four distribution centres across the UK, onshoring fasteners from Optimas allows UK manufacturers to satisfy these new requirements by sourcing parts closer to home.
Globally, our manufacturing facility in Illinois, USA, alongside our distribution centres in North America, Asia and Europe allow our partners across the globe to nearshore or onshore their supply, wherever they are.
Onshoring also reduces lead times and minimises supply chain risk, meaning manufacturers can always rely on a steady stream of parts to meet demand.
Whether you produce standard or specialised automotive seating, Optimas can provide you with a reliable source of quality parts and components to suit your needs. Get in touch with us to maximise your product quality and meet demand.
Maintaining a Streamlined Supply
While manufacturing trailers using quality parts is key, to get these parts to a production line it’s crucial manufacturers maintain a streamlined supply chain.
A supply chain relies significantly on HGVs for the transportation of goods, but the demand for manufacturing HGVs and trailers is increasing, as businesses struggle to source the parts to produce them.
The past couple of years have highlighted the importance of onshoring and nearshoring, as evidenced by the number of manufacturers opening up new plants nearer their customer base. Not only does onshoring ensure a steady and reliable stream of parts, but it also lowers manufacturers’ carbon footprints, as fasteners require minimal transportation.
With fastener distribution centres all over the globe and cold-form manufacturing facilities on both sides of the Atlantic, we’ve partnered with manufacturers for over 100 years helping them to meet demand by sourcing quality parts, closer to home.
Alongside our offering of both standard and specialised fastening solutions, our OptiTech VMI solutions ensure our partners receive their parts on time, every time, using advanced cloud-based technology. With manufacturing, distribution and engineering all under one roof, we can help you streamline your supply chain and optimise your product quality.