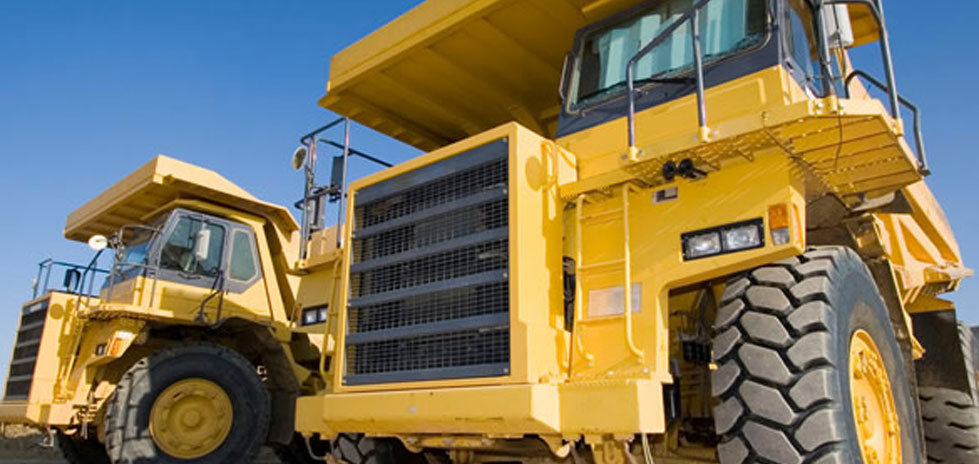
Verbund-Elektrobusse der nächsten Generation fahren mit Optimas-Befestigungselementen
Vor allem China war ein früher Anwender von Elektrobussen, aber jetzt nimmt der Trend weltweit zu. Mit einem schärferen Fokus der Gesetzgebung und der Öffentlichkeit auf das globale Emissionsniveau, die Luftqualität in dicht besiedelten Gebieten und die Debatte um herkömmliche Dieselantriebe bieten elektrische Antriebe jetzt eine praktikable Alternative für den Betrieb öffentlicher Verkehrsmittel, ohne die Umwelt zu beeinträchtigen. Mit modernen Verbesserungen in der Batterietechnologie und Fahrzeugreichweite gewinnt der Elektrobus an Fahrt.
Der Umstieg auf eine völlig neue Generation von Antriebssträngen stellt OEM-Bushersteller vor einige große Herausforderungen. Zunächst einmal transportieren elektrische Antriebsstränge im Gegensatz zu einem Benzin- oder Dieselantrieb riesige Mengen an elektrischem Strom. Daher müssen Komponenten in diesen Fahrzeugen ordnungsgemäß isoliert werden, um sicherzustellen, dass keine Leitung zu anderen Teilen des Fahrzeugs auftritt und die Polarität umgekehrt wird.
Zweitens ist die Frage des Gewichts. Mit einer begrenzten Reichweite zwischen Ladestationen müssen Elektrobusse so leicht wie möglich sein, um die maximale Effizienz während der Fahrt zu bieten. Bei der Berücksichtigung der Passagiere wird deutlich, dass die Minimierung des Gewichts selbst der kleinsten Komponente von größter Bedeutung ist.
Geben Sie Zusammensetzungen ein. Die Fähigkeit von Verbundwerkstoffen, entsprechend robuste Baugruppen mit reduziertem Gewicht zu konstruieren, hat dazu geführt, dass sie zu einem festen Bestandteil von Rennwagen auf der ganzen Welt geworden sind. Bei elektrifizierten Fahrzeugen bedeutet geringes Gewicht jedoch nicht nur mehr Leistung, sondern auch mehr Reichweite.
Die dritte Herausforderung besteht darin, eine ausreichende Wissensbasis zu entwickeln, um eine völlig neue elektrifizierte Plattform zu entwickeln. Die Branche durchläuft derzeit einen Paradigmenwechsel hin zur Elektrifizierung, sodass viele Unternehmen möglicherweise keinen Zugang zu vorhandenem Fachwissen in Bezug auf Elektrofahrzeuge haben. Bei der Auswahl von Verbindungselementen für diese innovativen Plattformen kann es schwierig sein, den richtigen Experten zu finden, der die richtigen technischen Komponenten in angemessener Qualität liefert. Vor allem, wenn die Fertigungsstandards eher mit Rennteams als mit öffentlichen Verkehrsmitteln in Verbindung gebracht werden.
Aus diesem Grund wandte sich ein Bushersteller an das Know-how von Optimas Solutions, einem globalen Industrievertriebs- und Serviceanbieter, um bei der Spezifikation geeigneter Befestigungselemente für seine völlig neue modulare Buschassis-Plattform aus Verbundwerkstoffen zu helfen. Optimas gewinnt schnell den Ruf, die Muttern und Schrauben hinter einigen der wirkungsvollsten Elektrofahrzeuge zu liefern, die auf die Weltbühne kommen; und damit der ideale Partner für solche Projekte. Letztendlich erkannte der Hersteller die Notwendigkeit, von Beginn des Projekts an eine innovative Materialliste (Bill of Materials, BoM) zu definieren, die für das Composite-Chassis geeignet wäre.
Ian Larkin, Customer Application Engineer bei Optimas, über das Projekt: „Wir wurden ursprünglich von einem Drittanbieter, einem bestehenden Hardware-Distributor des Busherstellers, gebeten, an dem Projekt teilzunehmen. Dieser Lieferant liefert Standardteile zur Unterstützung der Fertigung bestehender Busmodelle; Sie baten um unsere Mithilfe, um bei der Elektrobusplattform zu helfen. Insbesondere wurden wir gebeten, bei der Entwicklung einer Reihe von Standards für Verbindungselemente zu helfen und spezielle Konstruktionen von Verbindungselementen zu identifizieren. Wir arbeiten oft mit OEM-Herstellern und Zulieferern zusammen, um bei der Entwicklung von Verbindungselementen zu helfen, also machen wir uns an die Arbeit mit den gemeinsamen Engineering- und Designteams.“
Das Design des neuen Busses ist eine Premiere für die Branche. Das modulare Verbundchassis des Busherstellers umfasst einen großen Speicherbereich für Batteriemodule, der sich unter der Karosserie befindet, gekoppelt mit einem vorderen und hinteren Hilfsrahmensystem. Diese Anordnung wird mit Hochleistungsautos in Verbindung gebracht, aber ihre vorteilhafte Kombination aus verbesserter Kraftverteilung im gesamten Fahrgestell und reduziertem Gewicht eignet sich hervorragend für die Anwendung bei Elektrobussen.
„Wir konnten eine Liste von Standardteilen für den Bau der Prototypbusse definieren, die wir aus unserem globalen Portfolio von Komponentenherstellern ausgewählt haben“, fährt Ian fort. „Um dies zu erreichen, haben wir die Komponenten für dieses Projekt mit den Befestigungsstandards abgeglichen und auf Komponenten verwiesen, die bereits für den Bau der ersten Prototypbusse ausgewählt wurden. Am Ende konnten wir 162 einzelne Teilenummern zur Stückliste liefern, einschließlich Muttern, Bolzen, Schrauben und Unterlegscheiben. Nachdem diese Teile in einem kontrollierten Bauprozess hinzugefügt wurden, konnte der Hersteller 5 Prototypen herstellen. Anschließend brachte das Unternehmen den neuen Elektrobus nach Abschluss der Tests auf den Markt.
„Befestigungselemente für Elektrofahrzeuge zu spezifizieren, ist eine Herausforderung, vor der viele OEM-Fahrzeughersteller derzeit stehen, und es ist eine Herausforderung, der sie sich stellen müssen, um sicherzustellen, dass sie der Branche einen Schritt voraus sind. Durch die Nutzung unserer Erfahrung mit Lieferanten von Verbindungselementen im Transport- und Automobilsektor sind wir mit Lösungen vorbereitet. Bei der Entwicklung hin zu emissionsarmen und voll elektrifizierten Fahrzeugen vergisst man leicht, dass nicht nur der Antriebsstrang enorm weiterentwickelt wird, sondern auch die dazugehörigen Befestigungselemente und Baugruppen.“
Erfahren Sie mehr über unsere Technische Dienstleistungen.