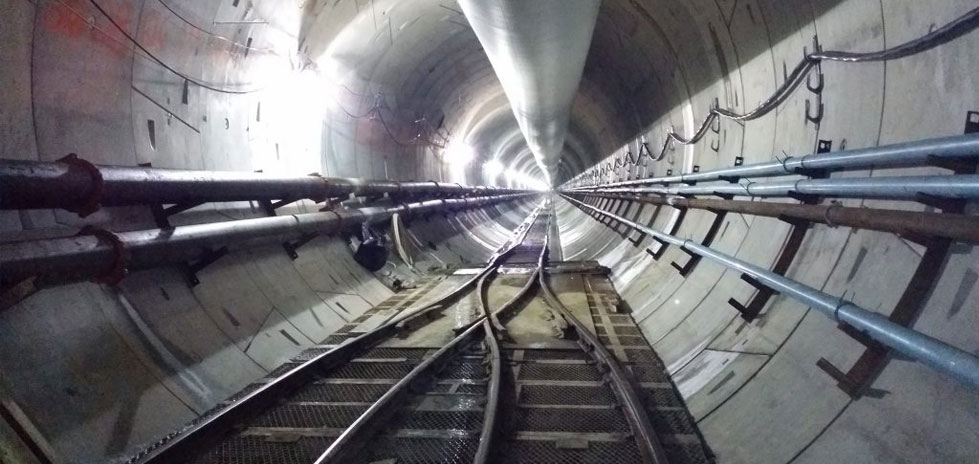
Il tuo tunnel non è come quello di chiunque altro: perché riparare i tuoi componenti dovrebbe essere?
Le gallerie sono tra i progetti di ingegneria civile più difficili e complessi. Pertanto, anche i sistemi standard di connessione e allineamento richiesti per collegare le sezioni del tunnel sono altamente ingegnerizzati. Tuttavia, alcuni progetti di tunnel presentano sfide uniche che le parti standard non sono attrezzate per far fronte. La Divisione tunnel di Optimas Solutions sa che la riprogettazione delle soluzioni esistenti per soddisfare determinate esigenze o lo sviluppo di prodotti nuovi di zecca può fare molto per migliorare le attività di costruzione del tunnel e il risultato finale.
Sandrine Ordener, direttore tecnico della divisione tunnel di Optimas Solutions, spiega come il vostro progetto può trarre vantaggio dalle soluzioni ingegnerizzate di fissaggio del tunnel.
Come abbiamo discusso in un precedente articolo, non esiste un progetto di tunnel standard. Ogni progetto presenta nuove sfide, basate su obiettivi finali, budget, posizione geografica, condizioni del terreno, pratiche locali e requisiti di sicurezza. Di conseguenza, i rivestimenti del tunnel devono corrispondere a queste condizioni per collegare in modo appropriato segmenti e anelli. Ciò significa che le soluzioni di fissaggio standardizzate non affronteranno sempre le sfide e le esigenze specifiche di un progetto di tunnel.
I componenti di fissaggio vengono utilizzati per collegare anelli e segmenti di tunnel separati, contribuendo a sostenere la resistenza dell'intera costruzione. Pertanto, le soluzioni di fissaggio dovrebbero aiutare a sigillare il tunnel dall'ingresso di acqua e impedire l'apertura degli anelli del tunnel o l'ovalizzazione del tunnel.
Numerosi aspetti possono rendere queste attività di installazione ancora più impegnative. Alcuni dei fattori che possono svolgere un ruolo importante includono condizioni locali come ambienti corrosivi o la probabilità di eventi sismici.
In tali casi, soluzioni di fissaggio del tunnel standard altrimenti affidabili possono essere soggette a guasti precoci, compromettendo successivamente la durata dell'intero tunnel. Ad esempio, i connettori standard potrebbero non essere in grado di resistere alla corrosione, all'equilibrio e alla flessibilità durante i terremoti o sopportare carichi elevati.
Al contrario, i componenti di fissaggio su misura sono concepiti per rispondere alle esigenze e alle sfide individuali di un progetto di tunnel, quindi funzioneranno secondo uno standard più elevato. Inoltre, le soluzioni chiavi in mano possono semplificare e accelerare la connessione di anelli e segmenti, migliorando la produttività in loco. Per personalizzare i componenti di fissaggio del tunnel, specialisti esperti come la Divisione tunnel di Optimas seguono un metodo rigoroso che garantisce la consegna di parti idonee di alta qualità in modo conveniente ed economico.
Il processo alla base dei servizi personalizzati di fissaggio del tunnel
Il processo di ottimizzazione o innovazione di un componente di fissaggio del tunnel inizia con una richiesta del cliente. In questa fase, la comunicazione e il feedback sono fondamentali per comprendere le esigenze uniche di un progetto. Un produttore esperto di soluzioni di fissaggio a tunnel utilizzerà queste discussioni iniziali per identificare se un componente standard si adatterebbe o se fosse necessaria una soluzione su misura. Inoltre, lo specialista può quindi determinare se una semplice riprogettazione o ottimizzazione di un componente esistente può essere sufficiente o se sono necessarie parti nuove di zecca innovative.
Ad esempio, per affrontare le sfide della costruzione di gallerie in ambienti corrosivi come nel progetto IDRIS (Inner Doha Resewage Implementation Strategy) in Qatar, la Divisione Tunnel di Optimas ha utilizzato la sua esperienza per ridisegnare un sistema di stuccatura standard, adattando il polietilene ad alta densità (HDPE) ) in-liner e aumentano la resistenza del rivestimento e la sua durata.
Sulla base della valutazione iniziale e delle specifiche del progetto concordate, la fase successiva del processo di innovazione è quella di produrre un concetto di design per il componente personalizzato. Durante questa fase, vengono definiti materiali, forme e caratteristiche aggiuntive. Successivamente, i team di ingegneri testano la validità del progetto iniziale eseguendo simulazioni virtuali (in silico testing), ad esempio analisi agli elementi finiti.
Una volta che il modello teorico è stato dimostrato efficace, vengono create prove iniziali di concetto e prototipi con stampa 3D o altri metodi di prototipazione rapida. Questi vengono quindi utilizzati per condurre test di laboratorio e di vita reale per valutare le proprietà del componente, dimostrando la sua capacità di soddisfare i requisiti iniziali del cliente.
Non sorprende che i protocolli per i test non siano standardizzati in quanto i requisiti dei test varieranno notevolmente a seconda delle specifiche del progetto stabilite nelle fasi di pianificazione iniziale. Pertanto, il produttore dovrebbe lavorare a stretto contatto con il cliente per definire quali test sono richiesti. Per garantire la consegna di una soluzione di alta qualità, possono essere applicati specifici standard di qualità, anche se non è richiesta alcuna certificazione.
Ad esempio, i team specializzati della divisione tunnel di Optimas aderiscono agli standard di qualità ISO 9001. Inoltre, la società ha definito il proprio sistema di controllo qualità-controllo qualità (QCQA) per i suoi prodotti Sofrasar. Il sistema QCQA monitora l'intera produzione e i processi della catena di approvvigionamento, dall'approvvigionamento delle materie prime alla consegna ai clienti. All'interno del framework QCQA di Optimas, ogni contratto include una vasta documentazione, come schede tecniche, elenchi di progetti precedenti, certificati di consegna e liste di imballaggio.
Sulla base dei risultati ottenuti, la progettazione dei componenti o il metodo di produzione possono essere ulteriormente ottimizzati, al fine di migliorare le prestazioni del prodotto o la ripetibilità e riproducibilità del processo di fabbricazione. Una volta raggiunto il progetto finale ottimale del componente, il produttore creerà un nuovo codice univoco che identificherà il componente e procederà alla produzione e alla fornitura dei primi lotti.
Esperti esperti di componenti per tunnel possono fornire componenti personalizzati di alta qualità in breve tempo, al fine di consentire una costruzione agile del tunnel. Generalmente, l'intero processo di sviluppo può essere completato entro uno o due mesi, per la modifica di componenti esistenti, o tra otto e 24 mesi per la creazione di soluzioni innovative, poiché sono necessari ulteriori test.
Le diverse fasi della realizzazione di componenti su misura richiedono competenze e gamme di competenze diverse. Ciò significa spesso che i clienti devono contattare diverse parti in merito a consultazioni sulle specifiche dei componenti, progettazione, prototipazione, test e fabbricazione del prodotto finale. Aziende specializzate come la Divisione Tunnel di Optimas possono fornire un unico punto di contatto per tutte queste attività.
Facendo riferimento all'esempio sopra, grazie alle sue capacità ingegneristiche e produttive interne, la Divisione Tunnel di Optimas è stata in grado di produrre e fornire il sistema di stuccatura resistente alla corrosione richiesto dal progetto del tunnel di Doha, in Qatar.
Esperti specialisti nella riparazione di gallerie possono affrontare le sfide emergenti
Che si tratti di ottimizzare un componente esistente o di svilupparne uno nuovo, entrambi i processi presentano delle sfide. È compito del progettista gestire queste sfide e fornire una parte di alta qualità che mostra chiari progressi nelle prestazioni pur rimanendo economicamente fattibile per l'uso all'interno di un progetto commerciale.
Affrontare le sfide e trovare l'equilibrio può essere raggiunto fissando specialisti con una profonda conoscenza del settore delle gallerie, competenze avanzate sui prodotti e una conoscenza materiale e tecnologica per lo sviluppo continuo.
Dopo aver completato oltre 400 progetti, ora ci sono più di 500 prodotti standard nella gamma Sofrasar, ciascuno originariamente sviluppato per un'applicazione specifica. Optimas Sofrasar è proattivo e impegnato a supportare i propri clienti migliorando i componenti standard o sviluppando nuove soluzioni che soddisfano i requisiti dei singoli progetti di tunnel. La società ha oltre 20 anni di esperienza nel settore, quindi può facilmente comprendere e soddisfare le esigenze specifiche del progetto per qualsiasi costruzione di tunnel. Grazie all'ingegneria interna, alla produzione e alle strutture di collaudo di qualità, siamo in grado di fornire soluzioni di fissaggio durevoli di alta qualità che possono apportare grandi benefici al segmento della galleria, semplificando e accelerando l'assemblaggio migliorando le prestazioni generali.
Per saperne di più Divisione del tunnel.