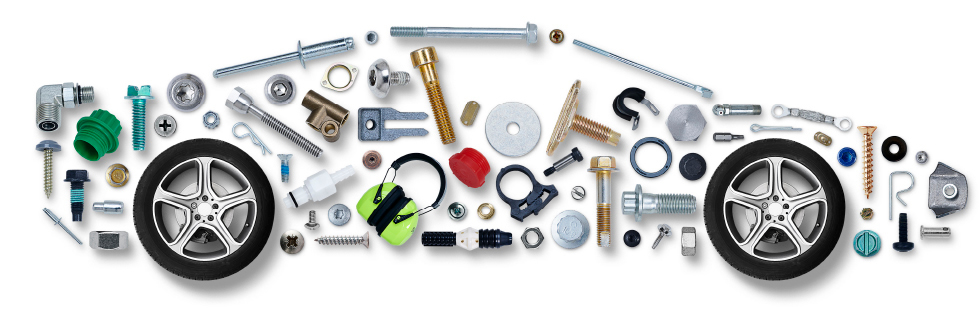
內飾,座椅和廢氣排放解決方案的全球製造商佛吉亞與Optimas合作定義了標準化的全球零件目錄,從而顯著提高了效率,節省了成本並加快了上市速度。
真實結果,真實影響
$1.8M
年度節省成本
79%
減少零件
82%
符合標準的零件
情況
佛吉亞依靠Optimas生產各種高質量的緊固件和C級零件。當像佛吉亞這樣的市場領導者不斷擴展其產品線時,這些低成本,大批量的零件就有可能使SKU激增。零件過多會導致成本增加以及多餘和過多的庫存。 Optimas認識到佛吉亞可以通過標準化的全球零件目錄來創建更高效的供應鏈,並加快其上市速度。
解
Optimas工程專家與佛吉亞(Faurecia)合作,精確學習瞭如何組裝產品和設計零件。 Optimas還引進了關鍵供應商來幫助開展這項合作,其中包括:
- 開發標準緊固件零件的全球目錄,以供多個程序使用
- 識別和消除陳舊和重複的零件
- 利用現有零件來滿足新的工程要求
- 由於工程團隊之間的緊密合作以及強大的供應商網絡,Optimas可以快速設計和採購佛吉亞的定制零件。
結果
通過在22個國家/地區的111家工廠實施全球標準,佛吉亞提高了質量,運營效率和財務績效:
- 降低總擁有成本 減少了79%的零件,提高了零件的規模經濟性,並減少了售前和售後零件的庫存
- 降低供應鏈風險 供應商少,庫存管理少
- 更快推出新產品,因為工程師可以從質量認可的標準產品列表入手,可以在世界任何地方快速訪問
Optimas以當地時區和貨幣向全球佛吉亞工廠部署了超過2億個全球標準零件。由於該計劃的成功,佛吉亞正在推出進一步的工藝優化。佛吉亞金屬與機電一體化全球商品總監Rainer Schulze說:“我們從Optimas的汽車內飾系統部門開始了這一旅程,此後將這一努力擴展到了我們的座椅和清潔出行業務部門。”佛吉亞擁有強大的實力和工程專業知識,有望通過不斷創新和商業成功來開展業務,並繼續改善其世界一流的產品。
“ Optimas零件標準化計劃不僅降低了我們的零件成本,而且還使我們能夠更快地推出新產品,減少庫存過時,提高產品質量並提高客戶滿意度。”
雷納·舒爾茲
全球商品總監
金屬與機電一體化
佛吉亞
下載案例研究