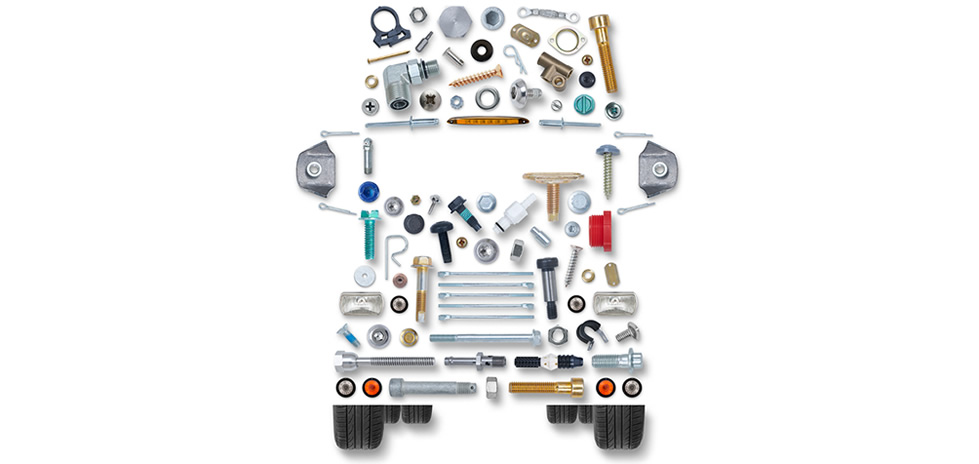
一家全球卡車製造商與Optimas合作,對通用生產平台的組件進行標準化,從而在產品生命週期內節省大量成本。
真實結果,真實影響
$5.9M
終生節省成本
275
零件消除
50%
更高的夾緊負載
情況
一家擁有兩個領先品牌的全球卡車製造商使用離散的緊固件零件單獨的物料清單,導致不必要的零件擴散,複雜性和成本。
解
Optimas工程師與製造商合作,從初始階段到開發,測試和生產,對組件進行標準化。通過參與整個計劃,Optimas專家可以儘早合理化組件策略,從而最大程度地降低了成本並提高了時間效率。
為了節省成本並簡化零件,Optimas確定了一個現有的接頭,該接頭具有昂貴且過時的鍍鎘尼龍鎖緊螺母和每種產品平台的混合電鍍工藝。 Optimas重新設計了接頭,使其包括一個重量更輕,更具成本效益的金屬防鬆螺母,並帶有特殊的面漆和用於所有三個組件的通用鍍層。
該解決方案可節省大量成本,並通過更可重複的扭矩張力關係提高了產品性能,改善了塗料附著力,沒有溫度限制,並且尼龍替代品具有更高的耐腐蝕性。較輕的防鬆螺母還允許更短的螺栓餘量,從而提高了燃油經濟性-這是商用卡車的主要問題。此外,聯合安裝不需要更改現有工具,並且引入後消除了275個零件號。
結果
Optimas緊固專家針對這兩個產品平台的標準化接頭設計和鍍層節省了大量資金,並提高了性能:
- 節省了$590萬的終生成本 並消除了多餘的庫存
- 夾緊負載增加50% 到22,500磅,並在240個小時的鹽霧下進行了標準化的腐蝕保護
- 消除了275個零件 品牌之間消除成本,風險和復雜性
- 重量減少10% 用金屬零件代替原來的尼龍零件
- 改進的裝配工藝 保持現有模具的同時,扭矩更小
“在整個生產過程中,重新設計和標準化此接頭可為兩個品牌節省大量成本,同時為客戶提高產品性能。”
史蒂夫·阿德金斯
北美工程總監
最佳質量
下載案例研究