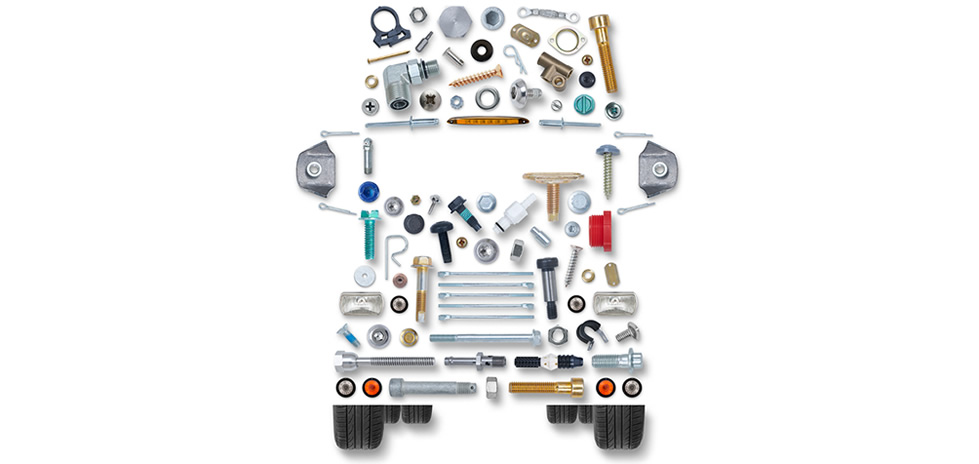
グローバルなトラック メーカーは Optimas と提携して、一般的な生産プラットフォームのコンポーネントを標準化し、製品の寿命全体にわたって大幅なコスト削減を実現しています。
本当の結果、本当の影響
$5.9M
生涯コスト削減
275
削除された部品
50%
より高いクランプ荷重
状況
2 つの主要ブランドを持つグローバル トラック メーカーは、個々のファスナー部品に個別の部品表を使用していたため、不要な部品の増殖、複雑さ、およびコストが発生していました。
解決
Optimas のエンジニアはメーカーと協力して、初期段階から開発、テスト、生産に至るまでコンポーネントを標準化しました。プログラム全体に関与することで、Optimas の専門家はコンポーネント ポリシーを早期に合理化し、コストを最小限に抑え、時間効率を高めることができました。
Optimas は、コストを削減して部品を簡素化するために、製品プラットフォームごとに高価で古風な、カドミウム メッキ、ナイロン ロックナット、および混合メッキ プロセスを特徴とする既存のジョイントを特定しました。 Optimas はジョイントを再設計し、3 つのコンポーネントすべてに特殊なトップコートと共通のメッキを施した、軽量で費用対効果の高い金属製ロックナットを含めました。
このソリューションは大幅なコスト削減と製品性能の向上を実現し、トルクと張力の関係の再現性が向上し、塗料の接着性が向上し、温度制限がなくなり、ナイロンの代替品から耐腐食性が向上しました。また、ロックナットが軽量化されたことで、ボルトの余裕が短くなり、商用トラックの大きな懸念事項である燃費が改善されました。さらに、ジョイント インストールは、既存のツールを変更する必要がなく、その導入により 275 の部品番号が削減されました。
結果
Optimas ファスニングの専門家による、両方の製品プラットフォームの標準化されたジョイント設計とメッキにより、大幅な節約とパフォーマンスの向上が実現しました。
- $590 万のライフタイム コスト削減を実現 余分な在庫を排除
- クランプ荷重を 50% 増加 22,500 ポンドまで、240 時間の塩水噴霧で正規化された腐食保護
- 275個のパーツを排除 ブランド間のコスト、リスク、複雑さを排除
- 10%の軽量化 オリジナルのナイロンパーツを金属パーツに交換することから
- 組立工程の改善 既存のツーリングを維持しながら、より少ないトルクで
「この接合部を再設計して標準化することで、両ブランドは大幅なコスト削減を実現しながら、顧客の製品性能を向上させることができました。」
スティーブ・アドキンス
北米エンジニアリングディレクター、
オプティマス
ダウンロード ケーススタディ