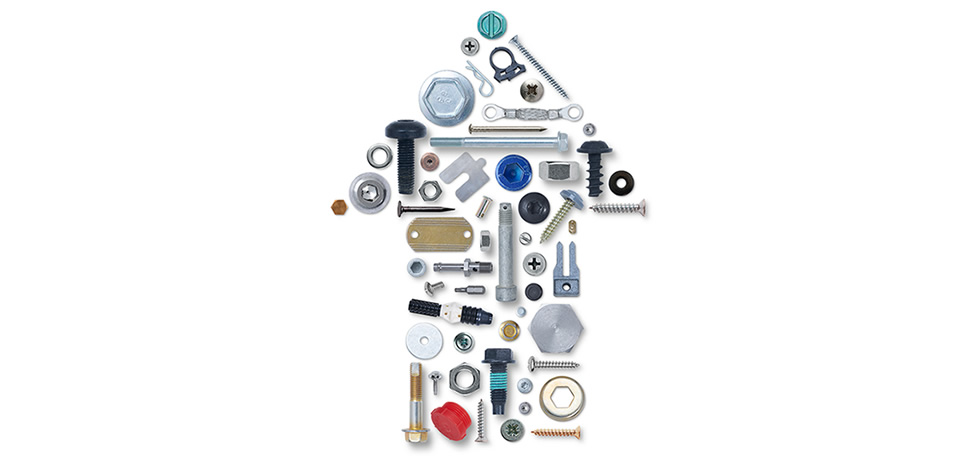
Binlerce farklı ürün üretilirken bileşen sayısını düşük tutmak zor olabilir. Özellikle, yeni bir ürün geliştirirken gerekli parçaların tekrarı meydana gelebilir.
Gerçek Sonuçlar, Gerçek Etki
28%
Parça Azaltma
332 bin
Tasarruf
Durum
Bir Fortune 500 motor ve güç üretim ürünleri üreticisi, yeni geliştirdiği jeneratörün üretim hattını iyileştirmek istedi. Bunu yapmak için tedarik zincirini daha verimli hale getirmek çok önemliydi. İlk Malzeme Listesi (BOM), 54'ü yeni ürün için gereken yeni parçalar olmak üzere 152 bağlantı elemanı ve C sınıfı bileşen içeriyordu.
Çözüm
Optimas, müşteriyle yakın bir şekilde çalışarak ihtiyaç duyulan toplam parça sayısını en aza indirmek ve mevcut bileşenlerin yeniden kullanımını en üst düzeye çıkarmak için ürün ağacını ve uygulamayı gözden geçirdi.
Sonuç
Bu yaklaşım sayesinde Optimas, ürün ağacını orijinal 152 bileşenden 109'a indirmeyi başardı. Mevcut bileşenleri kullanmak için yeniden tasarlama yoluyla, gereken 54 yeni parça yalnızca 15'e düşürüldü. Bu şekilde, üretici yalnızca $97'yi kurtarmakla kalmadı, Örnekleme ve hızlandırma maliyetlerinde 500, ayrıca parça oluşturma ve yönetim maliyetlerinde $234.000. Bugün Optimas, bu müşteriye dünya çapında 50'den fazla tesiste 11.000'in üzerinde benzersiz ürün ve yılda 359 milyondan fazla parça tedarik ediyor.