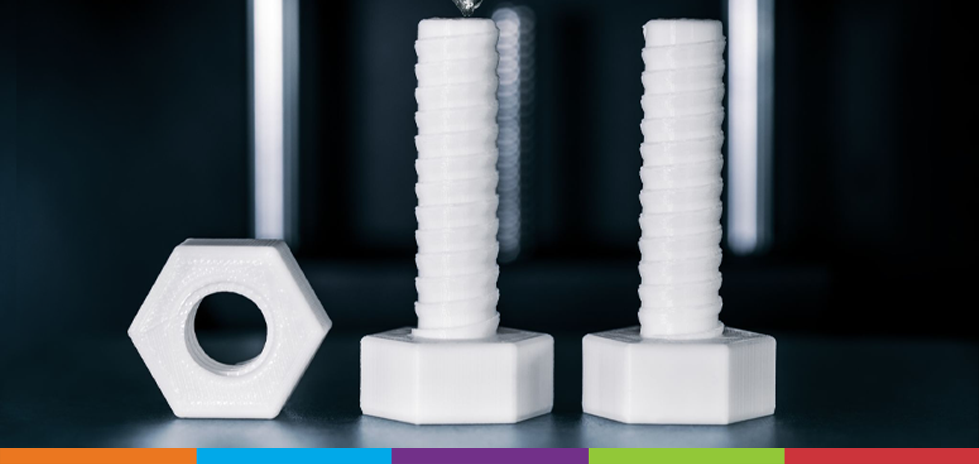
3 Schritte: Vom Prototyping zur Produktion
Vom Prototyping bis zur Produktion unterstützt Optimas Solutions globale Hersteller dabei, ihre Produktion zu steigern und in zahlreichen Branchen Kosten zu senken.
Mithilfe spezieller Prototyping-Geräte wie 3D-Druck und Automatendrehen arbeiten unsere hauseigenen Konstrukteure mit den Kunden von der Produktentwicklung bis zur Produktionslinie zusammen, um sicherzustellen, dass ihre Teile für den Einsatz optimiert sind, bevor sie in unserem Kaltschmiedeanlagen in den USA und Großbritannien.
Vom Prototyping bis hin zur Entwicklung und Produktion hochwertiger Verbindungselemente sind dies nur drei Schritte, die wir unternehmen:
1 – 3D-Druck
Die erfahrenen Konstrukteure von Optimas erarbeiten nach branchenspezifischen Anforderungen zuverlässige Befestigungslösungen gemeinsam mit den Kunden vor Ort oder auf Projektbasis.
Der 3D-Druck ist eine Methode, die Ingenieure nutzen, um schnell das Design und die Abmessungen eines Befestigungselements außerhalb seiner Anwendung zu überprüfen. Mit 3D-Druckern lassen sich Prototypen kundenspezifischer Teile in nur einem Tag erstellen. Es handelt sich also um einen äußerst effizienten Prozess.
Der 3D-Druck ermöglicht außerdem eine schrittweise Produktmontage, wodurch jeder Aspekt des Designprozesses transparenter wird. Hersteller benötigen häufig Spezialteile, und der 3D-Druck ermöglicht es Designern, präzise, geometrisch komplexe Prototypen zu erstellen.
Prototypen, die im 3D-Druckverfahren erstellt werden, sind zudem greifbar und voll funktionsfähig, sodass die Anwendungseignung eines Teils genau bestimmt und sein Design optimiert werden kann. Wenn das Teil als ungeeignet erachtet wird, kann am nächsten Tag ein neuer Prototyp gedruckt werden. Der 3D-Druck ist zudem kostengünstiger als herkömmliche Prototyping-Verfahren, da er nur sehr wenige Arbeitskräfte erfordert und der sehr geringe Abfall, der entsteht, vollständig recycelt werden kann.
2 – Automatendrehen
Nachdem das Design eines Produkts durch 3D-Druck optimiert wurde, kann das Teil anschließend durch Automatendrehen schnell und in geringer Stückzahl als Prototyp hergestellt werden.
Durch Automatendrehen erhalten Sie wichtige Informationen über die mechanischen Eigenschaften eines Teils, einschließlich Zugfestigkeit, Streckgrenze und Duktilität, um sicherzustellen, dass es am Einsatzort einwandfrei funktioniert und keine Mängel aufweist. Durch Automatendrehen können Sie nicht nur effizient und präzise Prototypen herstellen, sondern es fallen auch keine Werkzeugkosten für Teile in kleinen Stückzahlen an.
Das Automatendrehen zeichnet sich außerdem durch eine hohe Oberflächenqualität und präzise Abmessungen aus, wodurch eine übermäßige Bearbeitung im späteren Produktionsprozess vermieden wird.
Unsere Ingenieure sind nach IATF 16949 und ISO 9001:2015 zertifiziert und nutzen Qualitätsplanungssysteme, um Prozess- oder Produktrisiken im gesamten Produktionsprozess effektiv zu diagnostizieren, zu korrigieren und zu mindern.
3 – Kaltschmieden
Sobald ein Teil durch diesen strengen Testprozess optimiert wurde, kann es in unseren spezialisierten Kaltformanlagen in großen Stückzahlen hergestellt werden.
Kaltschmiedefertigung produziert besonders langlebige Verbindungselemente im großen Maßstab und ein erfahrener Hersteller von Kaltformmaschinen kann mit einer Genauigkeit von bis zu 0,02 mm arbeiten. Das bedeutet, dass Sie garantiert spezialisierte, qualitativ hochwertige Teile erhalten, die genau Ihrem Design entsprechen.
Optimas‘ Barton Cold-Form-Anlage in Droitwich, Großbritannien, hat sich mit Herstellern zusammengeschlossen, die eine unglaublich hohe Produktproduktion aufweisen. Mit 29 Kaltumformmaschinen von Nedschroef, Sacma und Nakashimada, die rund um die Uhr in Betrieb sind, ist Barton jedoch mehr als gut für die Produktion im großen Maßstab geeignet. Eine einzige Kaltumformmaschine kann Hunderttausende von Teilen pro Tag produzieren, was viel mehr ist als bei anderen Fertigungsformen wie Warmschmieden.
Wir verfügen über mehr als 90 Jahre Erfahrung darin, die kundenspezifischen Befestigungsanforderungen unserer Kunden zu erfüllen. Unsere integrierten Konstruktions- und Fertigungskapazitäten können Ihnen helfen, Ihre Produktleistung und -qualität zu verbessern. Ganz gleich, ob Sie standardmäßige oder maßgeschneiderte Befestigungslösungen benötigen, unsere Konstruktions- und Branchenkompetenz in Kombination mit unserem partnerschaftlichen Ansatz kann die Leistung Ihres Produkts optimieren. Kontaktiere uns jetzt um Ihre Produktionseffizienz zu maximieren.