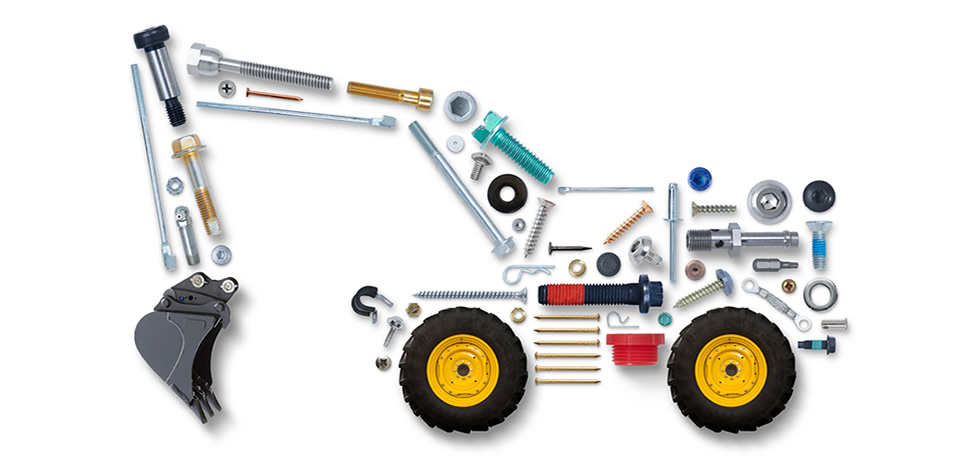
Caterpillar, ein weltweit führender Maschinen- und Motorenhersteller, ging eine Partnerschaft mit Optimas ein, um das Produktionsvolumen zu erweitern, Teilefehler zu reduzieren und die Produktzuverlässigkeit zu verbessern.
Echte Ergebnisse, echte Wirkung
3 ppm
Qualitätsleistung
95%
Verbesserung der Teilequalität
Lage
Caterpillar wandte sich an Optimas, um eine Anleitung zur Verbesserung der Produktzuverlässigkeit durch Reduzierung der Gesamtteilfehler von 60 PPM auf 30 PPM zu erhalten.
Lösung
Nach der Bewertung der Lieferkette und der Produktionsmethoden des Herstellers empfahl Optimas einen proaktiven Ansatz, um sicherzustellen, dass die Qualität während der gesamten Entwicklung, Produktion und Markteinführung von Produkten zu einer kritischen Komponente wird.
Die Qualitätsexperten von Optimas empfahlen die Übernahme von Toolsets aus dem Deutschen Qualitätsmanagementsystem-Standard (VDA 6.3) und dem Advanced Product Quality Planning (APQP) Framework der Automotive Industry Action Group (AIAG). Die vorgeschlagenen Best Practices erleichterten die Qualitätsplanung von Caterpillar im Voraus, ermöglichten eine pünktliche Produktionsbereitschaft und unterstützten die kontinuierliche Verbesserung, um die Kundenzufriedenheit sicherzustellen.
Optimas umfasste auch Layered Process Audits, um Kontrollen einzurichten, die mit qualitätskritischen (CTQ) Produktmerkmalen des Kunden verknüpft sind. Dieser prozessgesteuerte Ansatz ermöglichte es den Teileherstellern, die wichtigsten Aspekte ihrer Prozesse für die Verifizierung ins Visier zu nehmen. Um die APQP-Einführung abzuschließen, setzte Optimas das Framework in seiner Lieferkette ein, um sicherzustellen, dass alle Lieferantenpartner zum Qualitätsziel beitragen.
Ergebnisse
Mit einem umfassenden Plan, der darauf ausgelegt ist, alle Aspekte des Herstellungsprozesses zu beeinflussen, hat Caterpillar ein solides Qualitätsprogramm eingerichtet, das sich durch die gesamte Lieferkette zieht und:
- Reduzierte Teilefehler durch 95% auf 3 PPM von 60 PPM
- Qualitätsziel übertroffen von 30 PPM durch 90%
- Eliminiert fast alle Garantiekosten als direkte Folge von Teilfehlern
- Pünktliche PPAP-Lieferung von 100% erreicht für neue Produkteinführungen
„Das Optimas-Team hat seine beeindruckende Fähigkeit zur kontinuierlichen Qualitätsverbesserung bei lokalen Lieferanten und zur globalen Beschaffungskonsolidierung unter Beweis gestellt, was zu einer hervorragenden Qualitätsleistung geführt hat.“
David Zhang
Qualitätsmanager Beschaffung,
Logistikzentrum,
Raupe
Fallstudie HERUNTERLADEN