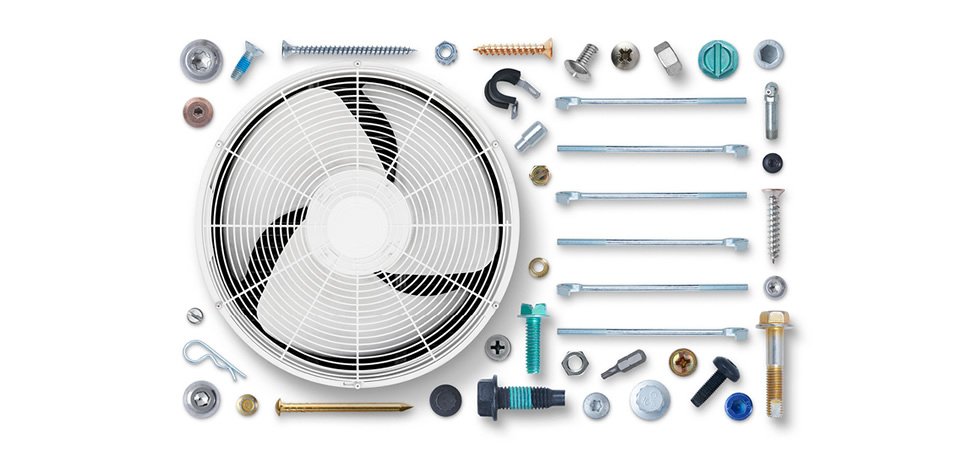
Ein Hersteller von kommerziellen Klimaanlagen hat sich mit Optimas zusammengetan, um einen elektrischen Steuerkasten neu zu konstruieren und die Teile- und Herstellungskosten erheblich zu senken.
Annualisierte reale Ergebnisse, reale Auswirkungen
$425,000
Innere Befestigung
Plattenbeseitigung
$60,000
Arbeit
Die Ermäßigung
$8,500
Schneckenkonsolidierung/
Beseitigung
Hintergrund
Ein bestehender Kunde lud Optimas ein, eine Initiative zur Kosteneinsparung in Bezug auf einen elektrischen Steuerkasten in einer gewerblichen Klimaanlage zu untersuchen. Frühere Innovationen konnten keine Befestigungslösung entwickeln, die zu Kosteneinsparungen führen würde.
Das ursprüngliche Design des Steuerkastengehäuses enthält eine große Stahlprägung zusammen mit einem Außengehäuse, das auf der Vorderseite des Schranks installiert ist. Dies wirkt als abgedichtete Einheit, um Lecks und Feuchtigkeit zu verhindern.
Die Innenplatte ist mit einer großen Auswahl an vorgestanzten Löchern konstruiert und hergestellt, um jede mögliche elektrische Komponentenkonfiguration aufzunehmen. Im Durchschnitt verwendete der Kunde nur 30% der Löcher, die in den elektrischen Steuerkasten eingebaut waren.
Herausforderung
Eine Initiative zur Kosten- und Arbeitsersparnis, die einen zu wenig genutzten Teil eines elektrischen Schaltkastens in einer gewerblichen Klimaanlage eliminiert.
Handlung
Entwerfen Sie ein Befestigungssystem im „Dimple“-Stil, einschließlich einer Reihe von scharfkantigen, gewindeformenden Schrauben, die bei Kontakt mit Wänden einrasten und:
- Entspricht den UL-Produktionsanforderungen
- Erleichtert den Montageprozess während der Fertigung
- Ermöglicht „Austausch“ im Feld
- Sorgt für einen wasserdichten Verschluss
Ergebnisse
- Das „Dimple“-Design eliminierte die Innenplatte des elektrischen Steuerkastens und bestand UL-, Wetter- und Transporttests.
- Neu gestaltete Schrauben verringerten das für die Installation erforderliche Drehmoment im Vergleich zu standardmäßigen gewindefurchenden Befestigungselementen.
- Beseitigung von Ablagerungen, die während des Gewindeschneidens/der Installation in der Fuge entstanden oder zurückgeblieben sind.
- Reparaturen vor Ort/zusätzliche Komponenten können mit Standard-Maschinenschrauben durchgeführt werden, die in vorhandene Gewinde eingebaut werden.
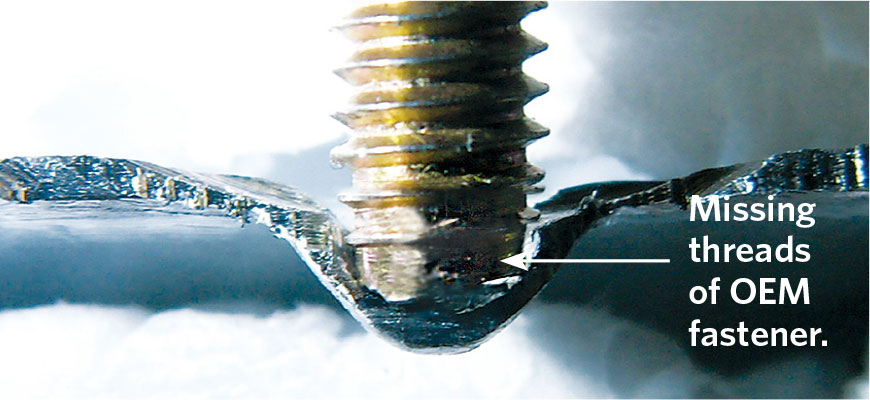
OEM-Befestigung: Eine Standard-Trilobularschraube kann nicht in eine Vertiefung eingreifen, die in die gestanzte Metallwand eines elektrischen Schaltkastens gedrückt wird.
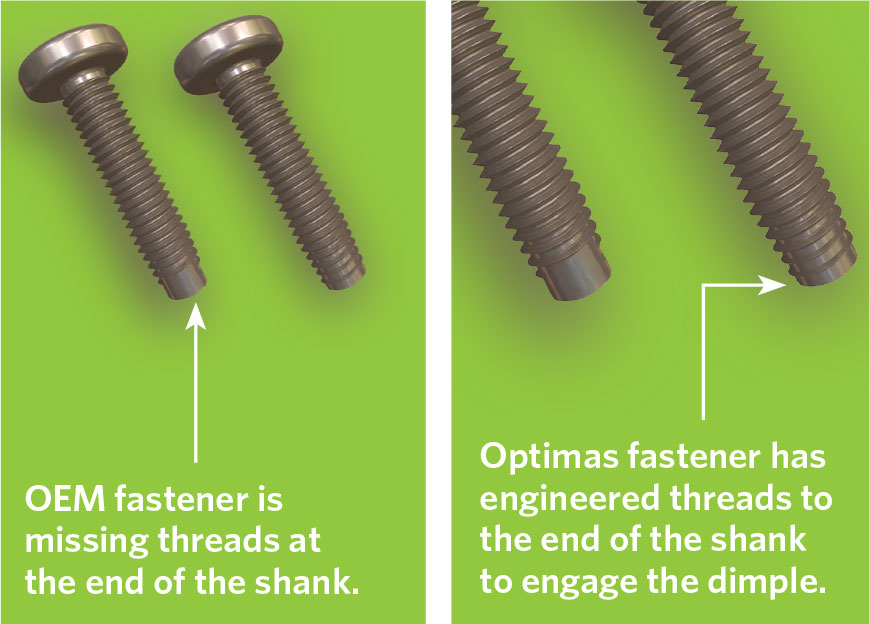
Neues Befestigungselement: Ersetzte eine trilobuläre, gewindeformende Schraube (links) durch eine trilobuläre, spitzkammige, gewindeformende Schraube (rechts), um in die Vertiefung einzugreifen.
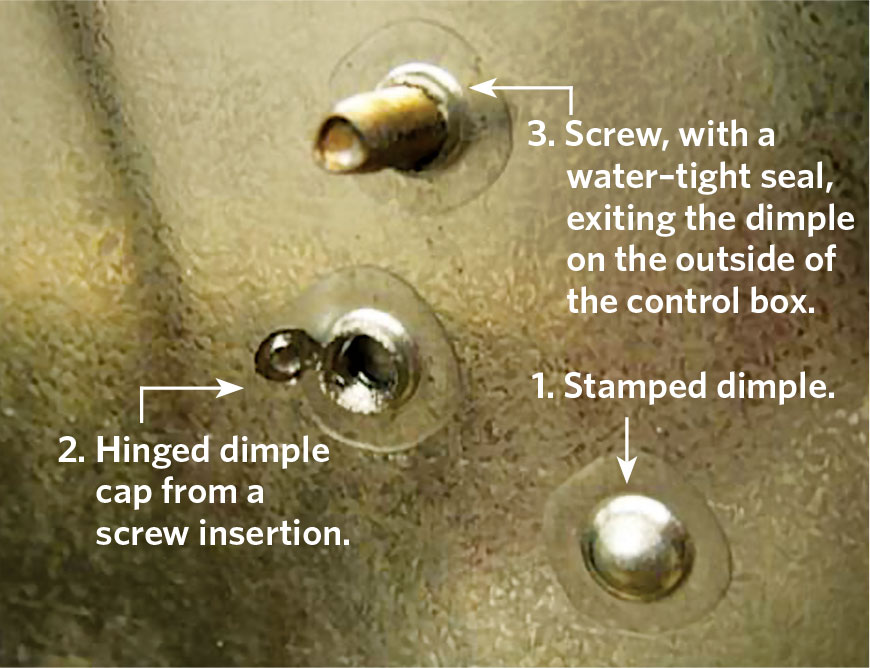
Optimas-Lösung: Befestigte Komponenten an der Innenwand eines elektrischen Schaltkastens und erfüllte alle Fertigungs- und Einsatzanforderungen.
Fallstudie HERUNTERLADEN