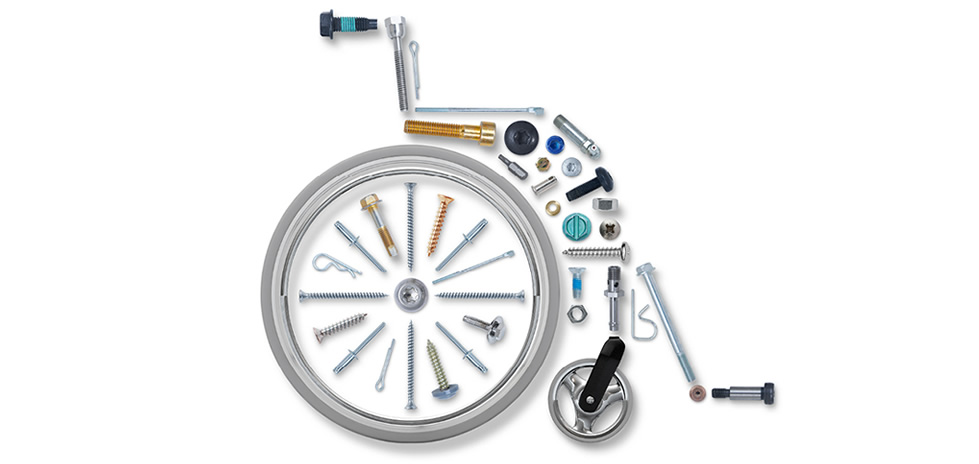
Als ein Hersteller medizinischer Geräte aufgrund von Bestandsproblemen an Produktivität verlor, implementierte das Optimas-Team ein Bestandsverwaltungssystem mit intelligenter Technologie, das die betriebliche Effizienz verbesserte und Kosten sparte.
Echte Ergebnisse, echte Wirkung
$70K
Gesamtkosteneinsparungen
30%
Reduzierung des Lagerbestands
87%
Erhöhte Lagerumschläge
Lage
Ein Hersteller langlebiger medizinischer Geräte verlor seine Produktivität aufgrund von Problemen bei der Bestandsversorgung. Ein manueller Prüfungsprozess und eine ineffiziente Teilebereitstellungsstrategie machten es schwierig, den Standort der Teile, die Anzahl der Teile und die Nutzung im Laufe der Zeit zu verfolgen. Infolgedessen kam es beim Hersteller zu überfüllten Lagerbeständen und Produktionsengpässen. Der Kunde wandte sich an Optimas, um sein Bestandsverwaltungssystem zu überholen und Ausfallzeiten zu beseitigen.
Lösung
Optimas implementierte ein kundenspezifisches Bestandsverwaltungsprogramm mit intelligenter Technologie, das eine klare Sichtbarkeit der Verbrauchsdaten ermöglichte, für betriebliche Effizienz sorgte und Kosteneinsparungen für den Kunden generierte. Durch den Übergang von einer direkten Linienzuführung zu einem Supermarkt-Ansatz konsolidierte Optimas den gesamten Bestand in einem zentralen Bereich, wodurch Teile leichter zu finden waren und gleichzeitig doppelte Teile, die an mehreren Standorten gelagert wurden, reduziert wurden. Jedes Teil wurde mit einem Kanban-System mit zwei Behältern eingerichtet und mit dem Inventar einer Woche bestückt. Optimas installierte die OptiRack VMI-Lösung, die fortschrittliche RFID-Technologie für die automatische Bestandsauffüllung verwendet. Innerhalb eines Monats hat Optimas das neue intelligente System schnell implementiert und den Hersteller geschult.
Ergebnisse
Mit einem ausgewogenen Lagerbestand und sofortigem Zugriff auf Teilestände und -verbrauch hat der Hersteller keine übermäßigen Lagerbestände oder Produktengpässe mehr. Ein effizienterer Betrieb führte beim 60% zu weniger Lagerplätzen und reduzierten Arbeitszeiten und Lagerhaltungskosten.
- Senkung der Gesamtbetriebskosten um $70.000
- Reduzierter Lagerbestand um 30%
- Erhöhung der Lagerumschläge um 87% (6 bis 26)
- Verringerte Lagerplätze um 60% (1.065 auf 428)
„Durch die Automatisierung des gesamten Prozesses wurde der Materialplaner von der Last der Teileverwaltung befreit, wodurch Zeit gewonnen wurde, um sich auf wichtigere Initiativen zu konzentrieren.“
Paul Pryzby
Vizepräsident und General Manager Optimas
Fallstudie HERUNTERLADEN