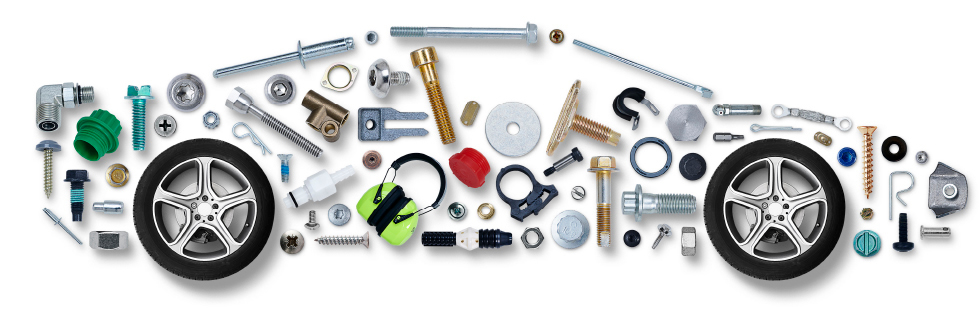
Ein renommierter Motorradhersteller wollte einen erfolgreichen Rennmotor in ein neues Rennrad einbauen und benötigte einen Befestigungspartner zur Unterstützung der Prototyping-Aktivitäten. OEM-Ingenieure lieferten eine vorläufige Liste mit 100 Teilenummern, die Optimas optimieren musste, um Kosteneinsparungen, technische Anforderungen und Markenästhetik zu erreichen.
Echte Ergebnisse, echte Wirkung
$2M
Jährliche Einsparungen bei Verbindungselementen
Lage
Die ursprüngliche Materialliste (BoM) gab keine Kopfformen, Materialqualitäten, Beschichtungen oder Eigenschaftsklassen an. Außerdem waren die Komponenten metrisch und nicht imperial, was die Herstellernorm war. Die Ingenieure von Optimas mussten mit jeder Iteration des neuen Fahrrads Schritt halten und die Spezifikation der Befestigungselemente optimieren, um während dieses kapitalintensiven Prozesses Materialkosteneinsparungen zu erzielen.
Lösung
Optimas empfahl eine Reihe geeigneter Standardbefestigungen, die aus seinem globalen Komponentenportfolio leicht verfügbar waren. Dies diente der Aufwandsminimierung und erfüllte gleichzeitig die wesentlichen Vorgaben hinsichtlich Ästhetik und Ingenieursleistung. Durch die enge Zusammenarbeit mit den Konstruktions- und Konstruktionsteams des Herstellers war Optimas in der Lage, die Richtlinien für Befestigungselemente im Handumdrehen aktiv zu gestalten, um mit dem einzigartigen Projekt Schritt zu halten.
Ergebnis
Einige Einzelkomponentenkosten wurden um bis zu 751 TP2T gesenkt, was dem Hersteller kumulativ eine jährliche Einsparung von 1 TP3T2 Millionen an Projektbefestigungen einbrachte.