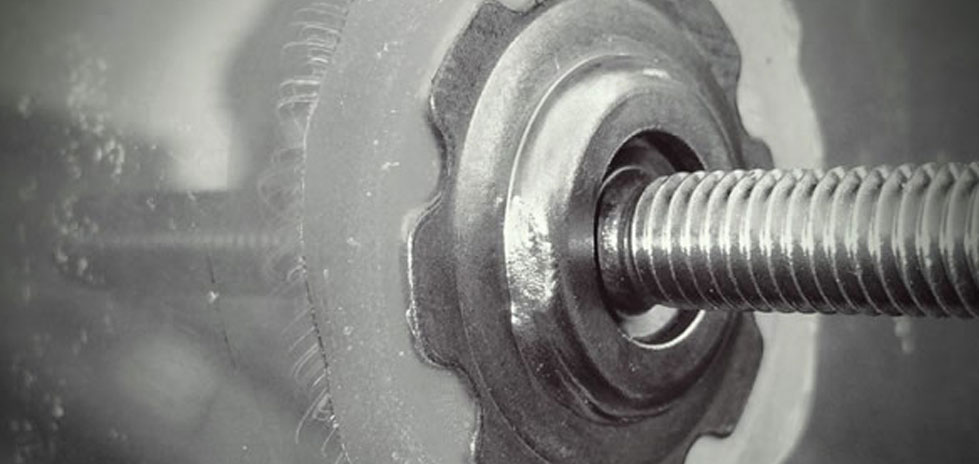
The Spida Stud from Optimas Components: A Strong, Lightweight Bonded Fastener
Optimas Components, a division of Optimas, has offered increased options for end users requiring adhesive bonded fasteners, with the addition of the Spida Fixings Spida™ Stud to its component range. Ideal for utilisation in aerospace, automotive and marine applications, the Spida™ Stud offers increased strength and improved adhesion properties to ensure a truly reliable lightweight bonded fastener.
Spida Fixings specialise in bonded fasteners. With the Spida™ Stud, the business has looked to improve performance while simultaneously reducing weight. This is of particular pertinence to the manufacture of vehicles, ships and aircraft, where the overall weight of fasteners can affect fuel economy and performance. The product’s inherent ease of installation also offers distinct benefits to manufacturers who work to tight production schedules.
New to the market, the Spida™ Stud offers a number of advantages over traditional bonded fasteners. First, the fastener itself is circumferentially welded to the back of the base, which reduces the risk of the fixing failing at the weld. This means that potential stresses are efficiently passed down the thread and dissipated out into the base of the fixing, greatly increasing the durability and ensuring the maximum possible breaking strength for a given fastener diameter.
Adhesion has also been an area of great focus for Spida Fixings. The base of the Spida™ Stud features eight self-levelling mini feet, which ensure an optimal 0.5mm bond line of adhesive is formed under the fixing. This consistent layer of adhesive underneath the fastener aids bonding. The feet also make for a castellated edge that improves torque resistance by 24%, enhancing the performance of the part in application. Coupled with a base featuring a large bearing area, load carrying capability is greatly increased. Furthermore, the base of the Spida™ Stud features a concave exothermic chamber, which serves to control the layer of adhesive securing the fastener. This construction enhances peel, shear, torsion, cleavage, tension and compression loading performance.
These features are paired with a proprietary surface treatment called AdMaxTM which increases the contact area for adhesive. The system mirrors the same principle as a gecko’s feet, with increased surface area delivering a stronger bond when installed. As a result, end users can benefit from up to a 54% increase in surface area to boost adhesion performance.
The stud itself is cold-forged by Barton, an Optimas company specialising in cold forging high-performance fasteners. Extensive length and diameter options mean that end users can select a component with the optimum strength for their application. Male and female threaded options are available, delivering increased specification versatility.
The Spida™ Stud is available in a number of materials depending on requirement. End users can specify marine 316L stainless steel, manganese and boron steel alloy, with further material options to be made available in the near future such as glass filled nylon and carbon fibre PEI lightweight engineering plastic. Other areas of variation include electroplated surface options, such as zinc nickel, which provides continuous salt spray protection for 678 hours. Further specialist surface treatment options are available by customer request.
In terms of adhesive, Spida Fixings can provide end users with guidance regarding the optimum choice for application.
Optimas Components Division can also supply a wide range of samples held in stock, offering end users the chance to assess the Spida™ Stud first hand. Furthermore, Spida Fixings can provide additional training and guidance regarding the component, ensuring optimum utilisation.
The Spida™ Stud range is now available via Optimas Components Division, who can quickly service orders of almost any size for delivery around the world. As a result, end users can benefit from the superior composite adhesion capabilities of the product on reduced lead times, backed by the component quality standards that define the business’ global outlook.