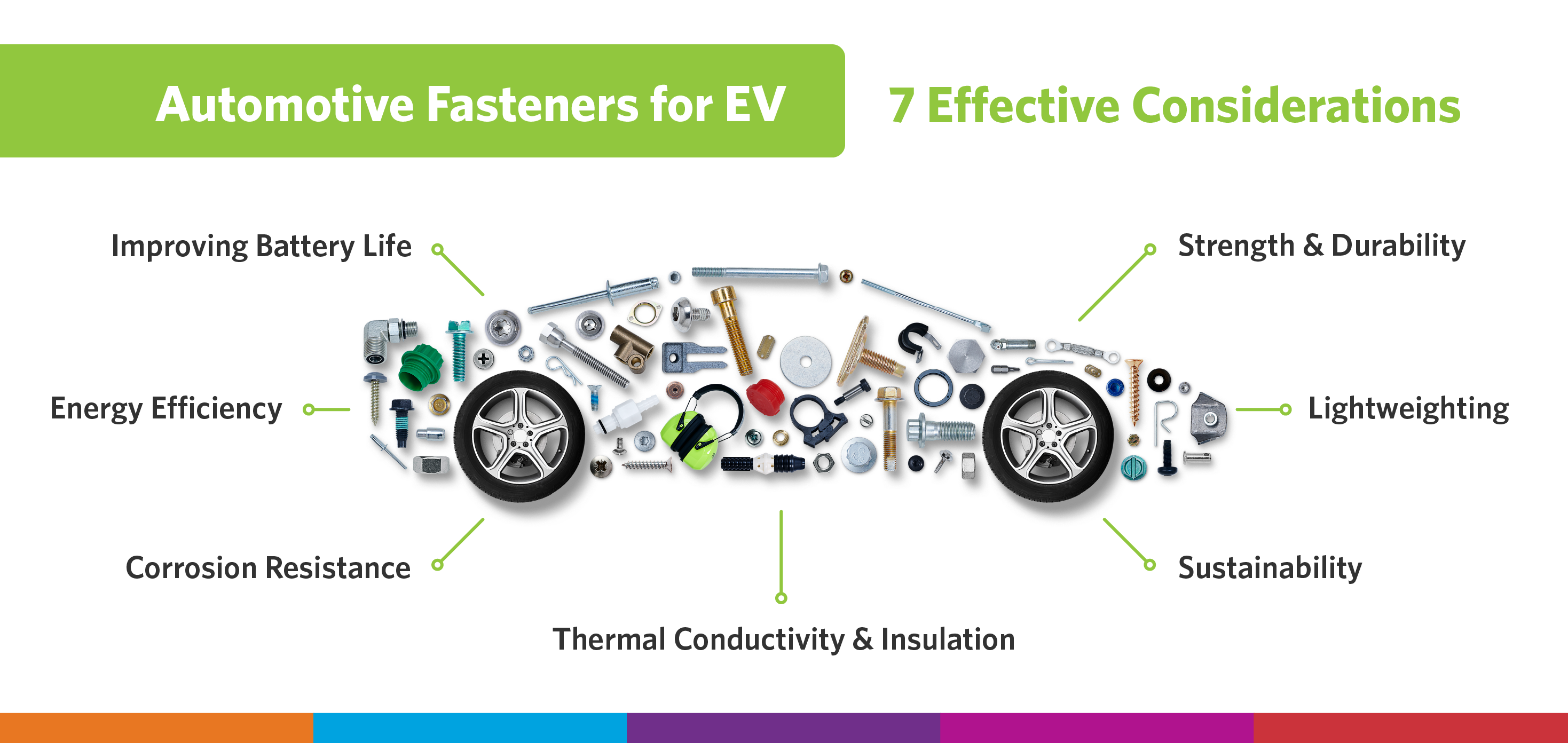
Automotive Fasteners for EV – 7 Effective Considerations
High-quality automotive fasteners are essential to produce a top electric vehicle (EV). Fundamentally automotive fasteners need to ensure all key components of an EV remain connected and secure. However, fastener experts can help EV manufacturers to identify the best fastening solutions to get the most performance out of their vehicles.
The global EV market is expected to grow at a CAGR of 15.71% from 2024-2029, suggesting that OEMs are preparing to cater to a transitioning consumer market. Therefore, EV manufacturers need to utilize the best parts, including fasteners, to give their products an edge over the competition.
Below are seven key considerations EV manufacturers can factor into their thinking when choosing the best automotive fasteners for their products:
- Strength and durability
- Lightweighting
- Corrosion resistance
- The impact on battery life
- Thermal conductivity and insulation
- Energy efficiency
- Sustainability
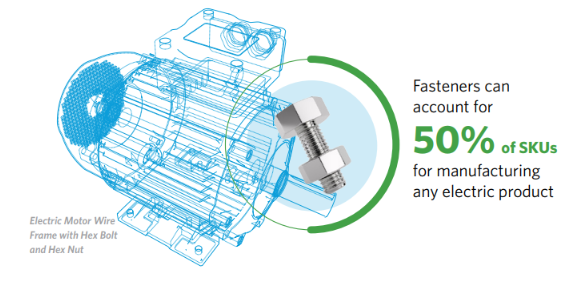
Optimas’ manufacturing divisions, located in the UK and US, and soon to be Mexico, specialize in producing standard, bespoke and licensed automotive fasteners across the EV build. Optimas specializes in cold-forming fasteners, a highly repeatable, cost-effective and scalable production process. As a result, Optimas’ automotive fasteners are ideally suited to EVs, prioritizing these key elements:
1. Strong and Durable Automotive Fasteners
- Cold forming maximizes a material’s metallurgical properties and structural integrity, prioritizing a part’s strength and durability. Fasteners must meet high tolerance and vibration demands, bearing loads between 65-90% of their yield strength so they don’t loosen or break in their installation or use. Optimas’ automotive fasteners are engineered and manufactured to ensure a very high level of safety and reliability for EVs, helping to support the integrity of the vehicle’s main structure.
2. Enhanced Performance for Your Automotive Fasteners
- Manufacturing is only becoming more advanced with the adoption of electric technologies. As EVs tend to be heavier than their petrol (gas) or diesel counterparts due to their batteries, using lightweight materials at every opportunity is crucial to heighten vehicle performance. Optimas has the capability to produce automotive fasteners for EVs in a wide range of lightweight materials, contributing to improved vehicle performance and fuel efficiency.
3. Corrosion Resistant Automotive Fasteners
- All vehicles, including EVs encounter moisture, cleaning chemicals and salt from gritted roads, so its automotive fasteners must be highly corrosion resistant. Aluminum, stainless steel and titanium provide excellent yield strength and are highly corrosion resistant, so these materials are well-suited for all automotive and EV applications.
- Picking the correct plating finish for the application can also help to mitigate the risks of corrosion. Galvanic corrosion must also be considered with the increasing use of aluminum and carbon fiber body panels in vehicles to help offset weight increases in vehicles.
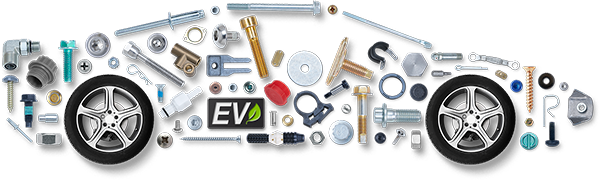
4. Lightweight Automotive Fasteners Can Improve Battery Life
- Using lightweight automotive fasteners for EVs also can help improve battery life. Lighter vehicles place significantly less strain on EV batteries, allowing for longer vehicle range and enhanced performance.
5. Automotive Fasteners Support Thermal Conductivity and Insulation
- EVs can generate a significant amount of heat during operations. If the vehicle’s fasteners and components aren’t optimized for use, this heat can transfer to critical components, risking low battery life and poor vehicle performance. Aluminum fasteners can help to dissipate heat buildup in EVs, in conjunction with dedicated heat sinks to help dissipate heat faster. It’s also critical that the automotive fasteners used for EV builds have a working temperature range suitable for operating in the temperatures generated.
- However, in other scenarios you will want thermally insulated fasteners to ensure they don’t operate as a thermal bridge. Drawing heat away from an area could lead to a potential buildup of condensation in electrically sensitive areas.
6. How Automotive Fasteners Can Help Improve Energy Efficiency
- Incorporating non-ferrous metals like aluminum, titanium or magnesium fasteners in any automotive build allows manufacturers to optimize their vehicles for energy consumption, ultimately enhancing the overall sustainability of the vehicle and leading to improved energy efficiency.
7. Optimas’ Sustainable Automotive Fasteners
- Evidently, the popularity of EVs is driven, among other things, by their eco-friendliness. So, it’s essential that OEMs source their fasteners from an eco-friendly manufacturer. Optimas’ manufacturing divisions in the UK and US have a firm and tangible commitment to sustainability.
- Additive waste produced by prototyping is recycled before a part is manufactured. Cold forming is also a highly sustainable production process, resulting in very minimal material waste.
In addition to manufacturing for EVs, Optimas application engineers can support your product build from project conception all the way to the production line. This can help streamline your current component selection and refine your EV BOM to help reduce costs. Click here to read about how Optimas helped an automotive partner save $400,000 by reducing their fastener BOM.
Get in touch with our experts to see how we can optimize your EV builds, as well as products from a range of industries.
Request a copy of our Electrification EBook
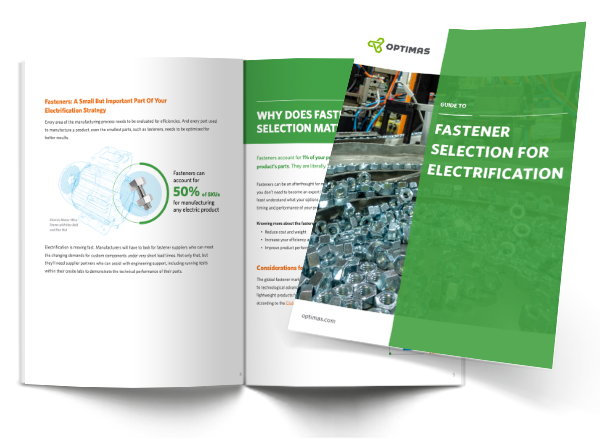