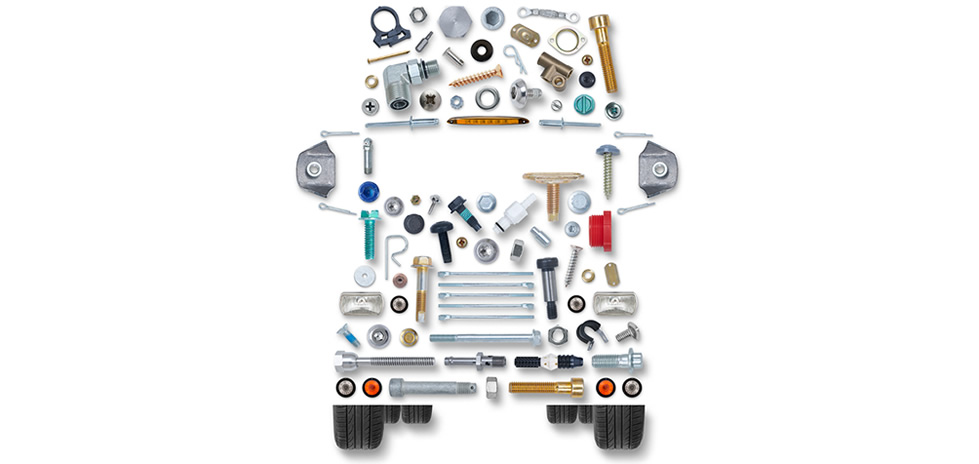
Optimas安普达 帮助全球卡车制造商完成通用生产平台组件的标准化,从而延长产品的使用寿命,节降了大量成本。
真实的结果,真实的影响力
$590万
节降的产品寿命所耗成本
275
较少的零部件个数
50%
提高的夹持能力
问题现状
一家全球卡车制造商拥有两个主导品牌,其使用不同的物料清单管理离散型紧固件,
致使不必要零件的激增,导致了产品的复杂性,提高了成本。
解决方案
Optimas安普达 的工程师与制造商合作,从最初阶段到产品开发、测试、生产,对组件进行标准化。Optimas安普达 专业人员的参与能够尽早的实现组件管理的合理化,从而将成本和交付时间降到最低。
为了节省成本并简化零部件,Optimas安普达 识别出一个成本昂贵、设计陈旧的镀镉接头,该接头使用尼龙防松螺母,并且每个产品装置仍采用混合电镀工艺。 Optimas安普达 重新设计了该接头,将重量更轻、成本更低的金属防松螺母与镀有特殊面漆、通用镀层的三个组件结合应用。
该解决方案显著节省了成本,提高了扭矩张力关系的可重复性,改善了涂料附着力,避免了温度影响,提高了防松螺母的耐腐蚀性,显著提高了产品性能。轻质的防松螺母还实现了更短的螺栓余量,从而提高了燃油经济性,解决了商用卡车的主要问题。此外,新接头的使用无需更改现有模具,较少了275个零部件。
成果分析
Optimas安普达 紧固专业人员,实现了接头设计的标准化并优化了产品装置镀层工艺,显著降低了成本,并提高了产品性能:
- 节省了590万美金的产品寿命所耗成本, 并消除了冗余库存
- 提升了50%的夹持能力 至22,500磅,并通过了240小时的盐雾标准防腐
- 消除了275个零部件, 降低了品牌成本,较少了风险和产品的复杂性
- 减少10%的重量, 用金属零部件替代了原先的尼龙零部件
- 改进了组装工艺, 在沿用现有模具的基础上,降低了扭矩
“Over a full production run, redesigning and standardizing this joint offered both brands significant cost savings while improving product performance for their customers.”
Steve Adkins,Optimas安普达 北美区域工程总监
下载案例分析