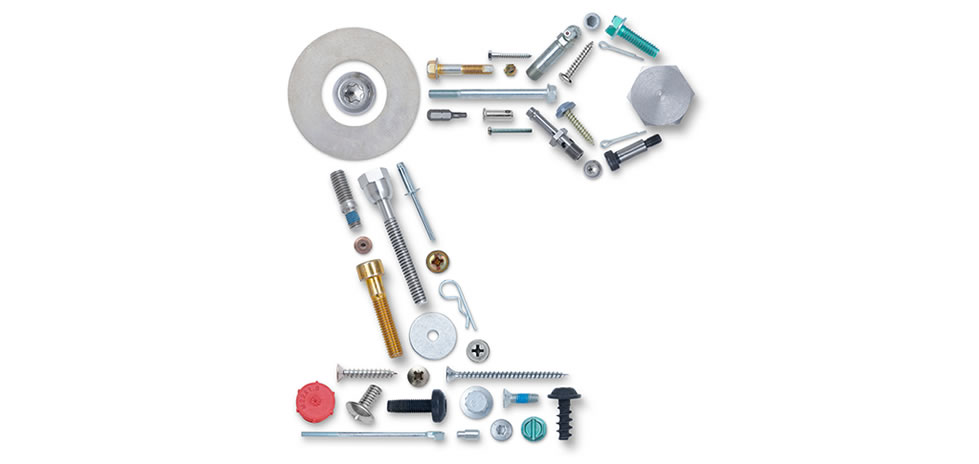
Wie ein globaler gewerblicher Garagentorhersteller mit Optimas zusammenarbeitete, um ein Teil neu zu konstruieren, das Ausfallzeiten eliminierte und Kosteneinsparungen brachte, ohne die Leistung zu beeinträchtigen.
Echte Ergebnisse, echte Wirkung
$120K
Jährliche Kosteneinsparungen
75%
Jährliche Kosteneinsparungen
Lage
Ein globaler Hersteller von gewerblichen Garagentoren beschaffte bearbeitete Messingkomponenten für einen seiner gewerblichen Überkopf-Toröffner. Als die Marktnachfrage stieg, führte der langwierige Herstellungsprozess zu langen Vorlaufzeiten, die zu Lagerengpässen und Produktionsausfällen führten.
Lösung
Das Optimas-Engineering-Team führte eine Produktzerlegung durch und ermittelte zwei Möglichkeiten zur Verbesserung des Bremsfedertellers aus Messing: Materialien und Herstellungsprozess. Während Messingteile Korrosionsschutz boten, belastete der Schraubprozess die Lieferkette zusätzlich. Der Lieferant hatte oft Mühe, die Produktionsanforderungen des Herstellers zu erfüllen.
Optimas empfahl einen kaltgeformten Ersatz aus kohlenstoffarmem Stahl mit einer galvanischen Zink- und klaren Chromatierung. Die Stahlalternative senkte die Teilekosten und erfüllte auch die Anforderungen des Herstellers an Korrosionsschutz während des Transports und der Teilehandhabung. Die Spezifikation eines kaltgeformten Bauteils brachte eine Vielzahl von Vorteilen mit sich, darunter ein vereinfachter Herstellungsprozess, weniger Abfall, kürzere Lieferzeiten und eine gesteigerte Produktionseffizienz. Die Herstellung konnte auch beginnen, ohne dass Konstruktionsänderungen an den Passkomponenten erforderlich waren, was während der Implementierung einen Mehrwert darstellte.
Ergebnisse
Durch die Beauftragung von Optimas als Experte für Befestigungselemente ging der gewerbliche Garagentorhersteller Lieferketten- und Anwendungsprobleme gleichzeitig an. Optimas lieferte Mehrwert und stärkte die bestehende Lieferkette durch die Neugestaltung einer einzigen Komponente:
- $120.000 gespart an jährlichen Kosten
- Reduzierte Teilekosten um 75% mit Stahlalternative, die den Korrosionsschutz beibehält
- Erhöhte Produktionseffizienz mit Kaltumformteil
- Leitungsunterbrechung beseitigt mit verbesserten Lieferzeiten
„Es kann einfach sein, überspezifizierte Komponenten zu identifizieren, Alternativen zu finden und die gewählte Lösung mit sehr geringen Störungen des bestehenden Betriebs zu implementieren. Ich denke, jeder, der mit Großserienfertigung zu tun hat, kann den Vorteil darin erkennen.“
Tim Tag
Techniker,
Optimas
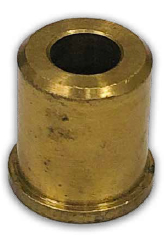
Vor
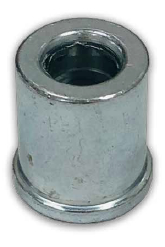
Nach
Fallstudie HERUNTERLADEN