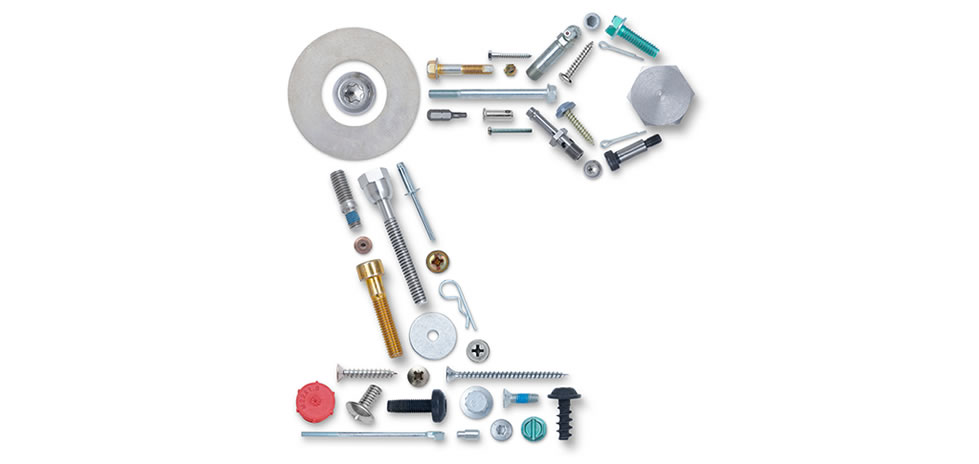
How a global commercial garage door manufacturer worked with Optimas to redesign a part that eliminated downtime and yielded cost savings without sacrificing performance.
Real Results, Real Impact
$120K
Annual Cost Savings
75%
Annual Cost Savings
Situation
A global commercial garage door manufacturer sourced machined brass components for one of its overhead commercial door openers. When market demand increased, the lengthy manufacturing process resulted in long lead times causing inventory shortages and production downtime.
Solution
The Optimas engineering team performed a product teardown and determined two opportunities to improve the brass brake spring cup: materials and manufacturing process. While brass parts offered corrosion protection, the screw machined process placed additional stress on the supply chain. The supplier often struggled to meet the manufacturer’s production demands.
Optimas recommended a cold formed low carbon steel replacement featuring an electroplated zinc and clear chromate finish. The steel alternative lowered part cost and also met the manufacturer’s requirements for corrosion protection during shipping and parts handling. Specifying a cold formed component delivered a host of benefits, including a simplified manufacturing process, less waste, faster lead times and increased production efficiency. Manufacturing could also commence without requiring design changes to any of the mating components, which added value during implementation.
Results
By engaging Optimas as a fastener expert, the commercial garage door manufacturer addressed supply chain and application problems simultaneously. Optimas delivered value and strengthened the existing supply chain through the redesign of a single component:
- Saved $120,000 in annual costs
- Reduced part cost by 75% with steel alternative that maintained corrosion protection
- Increased production efficiency with cold formed component
- Eliminated line disruption with improved lead times
“It can be straightforward to identify over-specified components, source alternatives and implement the chosen solution with very little disturbance to existing operations. I think anyone associated with large-scale manufacturing can see the benefit of that.”
Tim Day
Engineer,
Optimas
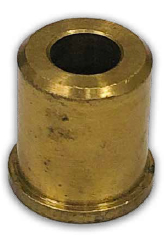
Before
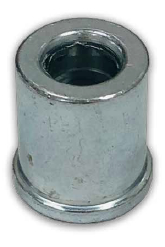
After
DOWNLOAD Case Study