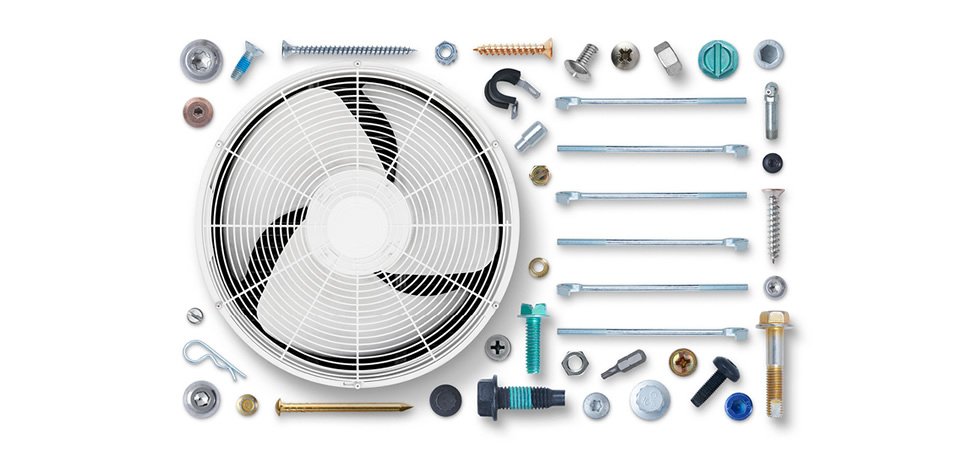
A commercial air conditioning manufacturer partnered with Optimas to re-engineer an electrical control box and significantly reduce part and manufacturing costs.
Annualized Real Results, Real Impact
$425,000
Inner Mounting
Plate Elimination
$60,000
Labor
Reduction
$8,500
Screw Consolidation/
Elimination
Background
An existing customer invited Optimas to explore a cost saving initiative relating to an electrical control box in a commercial air conditioning unit. Prior innovation failed to develop a fastening solution which would yield cost savings.
The original design of the control box enclosure contains a large steel stamping along with an outer casing that is installed on the face of the cabinet. This acts as a sealed unit to prevent leaks and moisture.
The internal plate is designed and manufactured with a large range of pre-pierced holes to house every potential electrical component configuration. On average, the customer only used 30% of the holes built into the electrical control box.
Challenge
A cost–and labor–savings initiative that eliminated an under–used part of an electrical control box in a commercial air conditioning unit.
Action
Design a “dimple” style fastening system, including a range of sharp-crested, thread–forming screws, that engages on contact with walls and:
- Adheres to UL production requirements
- Eases the mounting process during manufacturing
- Allows for “change outs” in the field
- Ensures a watertight seal
Results
- “Dimple” design eliminated the electrical control box inner panel and passed UL, weather and transit testing.
- Re-designed screws lowered the torque required for installation compared to standard thread-forming fasteners.
- Eliminated debris created or left in the joint during thethreading/installation.
- Field repairs/additional components can be made with standard machine screws installed into existing threads.
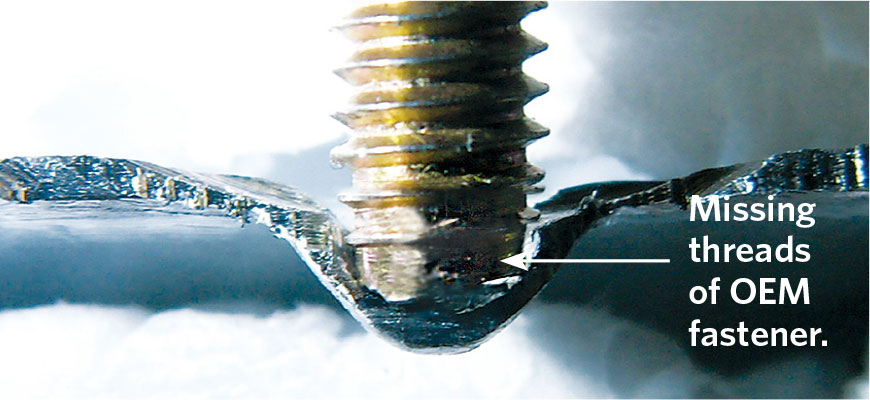
OEM Fastener: A standard trilobular screw can’t engage with a dimple pressed into the stamped metal wall of an electrical control box.
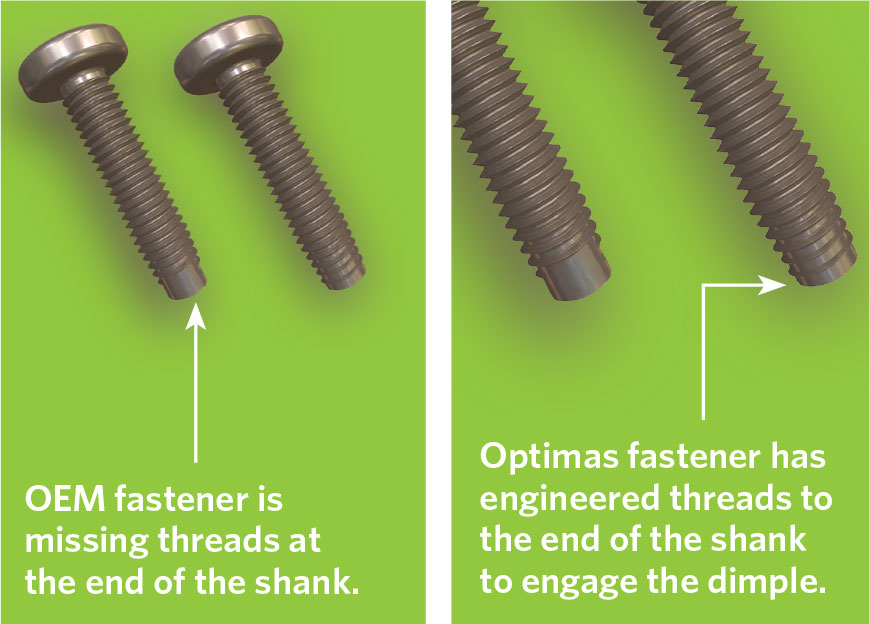
New Fastener: Replaced a trilobular, thread–forming screw (left) with a trilobular, sharp–crested, thread–forming screw (right) to engage the dimple.
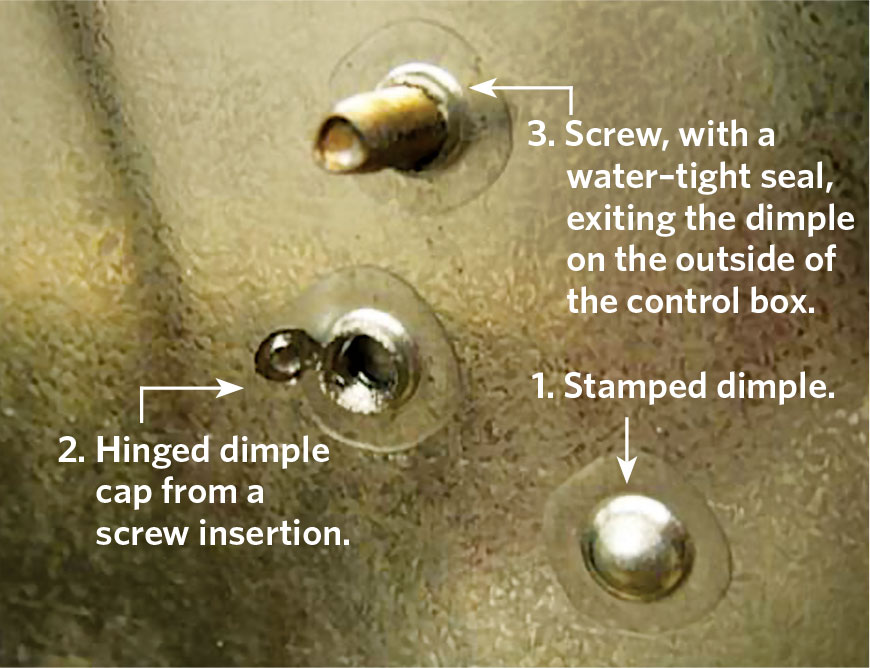
Optimas Solution: Fastened components to the inside wall of an electrical control box and met all manufacturing and field-use requirements.
DOWNLOAD Case Study