Industrial Fastener Distributor
and Manufacturer
Count on Optimas to reduce your total cost of ownership, minimize supply chain risk and increase efficiency.
Full-Service Supply Chain Solutions
with Regionalized Support
Ensure you have the right fastening solutions, with billions of parts delivered annually, to increase productivity and profitability.
Manufacturing + Distribution + Engineering
Optimas manufactures, sources and engineers industrial fasteners for customers globally. Lean on over 100 years of fastener and supply chain experience by starting a conversation with one of our knowledgeable industry experts today.
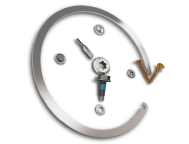
Minimize Supply
Chain Risk
Stay competitive with a streamlined supply chain, targeted sourcing and readily available inventory.
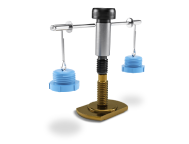
Optimize
Inventory
Review consumption, automate replenishment and reduce inventory with tech-enabled, just-in-time processes.
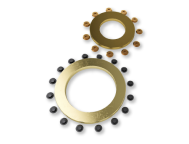
Enhance
Operations
Improve design and yield
while decreasing costs
within your facilities with Optimas engineers.
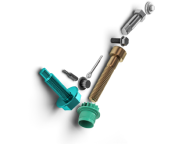
Improve
Quality
Rely on certified products, backed by in-house quality labs, and a zero-defect culture.
Learn More
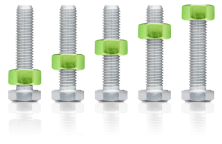
Drive Impact with a Full-Service Fastener Partner
We create value across the entire manufacturing enterprise by focusing on total cost of ownership. This includes understanding demand and consumption, ensuring availability and minimizing hidden costs.
Find the Expert Resources You Need
Explore the Optimas library of blogs, case studies,
podcasts, technical resources, videos and more.
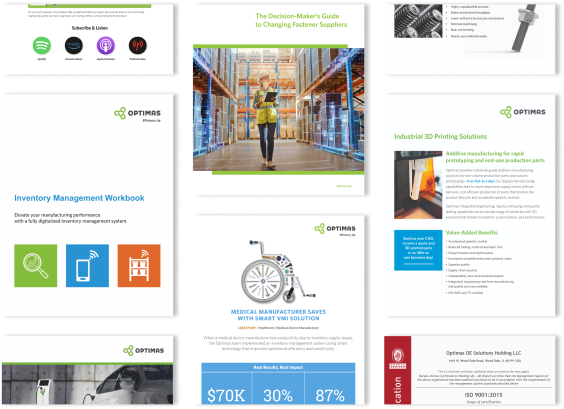