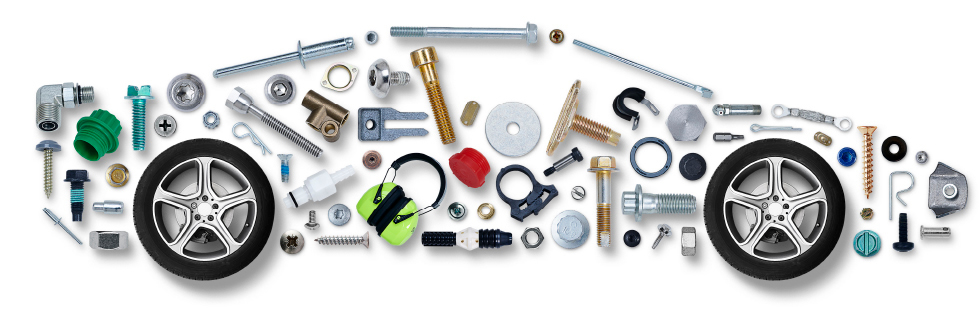
A prestigious motorcycle manufacturer wanted to incorporate a successful racing engine into a new road bike, and required a fastener partner to support prototyping activities. OEM engineers supplied a provisional list of 100 part numbers, which Optimas was required to streamline to achieve cost savings, engineering requirements and brand aesthetics.
Real Results, Real Impact
$2M
Annual Fastener Savings
Situation
The original Bill of Materials (BoM) did not specify head styles, material grades, plating or property class. In addition, the components were metric rather than imperial, which was the manufacturer norm. Optimas engineers were required to keep pace with each iteration of the new bike, streamlining fastener specification to deliver BoM cost savings throughout this capital-intensive process.
Solution
Optimas recommended a number of suitable standard fasteners that were readily available from its global component portfolio. This served to minimize expenditure, while also achieving the key provisos regarding aesthetics and engineering performance. Through working closely with the manufacturer’s engineering and design teams, Optimas was able to actively shape fastener policy on the fly to keep pace with the unique project.
Result
Some individual component costs were slashed by up to 75%, which cumulatively delivered an annual saving of $2 million on project fasteners to the manufacturer.