Inventory Management Resources
Customized vendor managed inventory (VMI) programs enable manufacturers to establish automated fastener replenishment cycles. Our innovative OptiTech Inventory Management Solutions blend secure technology, market forecast and consumption data and just-in-time (JIT) processes to optimize inventory levels for production, which increases efficiency and output.
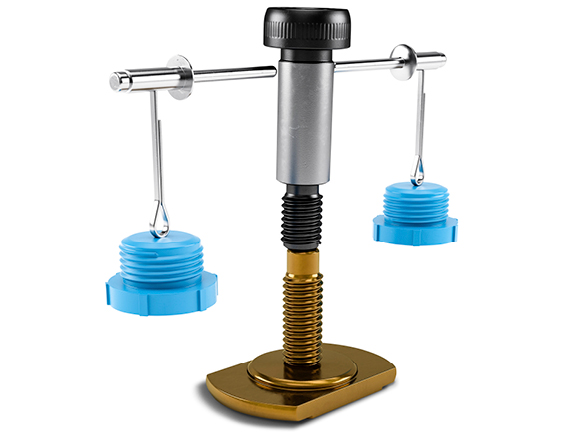
Optimas Customer Success Metrics
The Optimas part standardization program not only reduced our piece part costs, but it also enabled us to launch new products quicker, decrease inventory obsolescence, improve product quality and increase customer satisfaction.
– Rainer Schulze, Global Commodity Director, Metals & Mechatronics, Faurecia

How does improved supply chain visibility help
manufacturers make better data-driven decisions?
These Optimas Resources Can Help
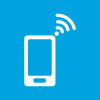
Are You Unable to Anticipate Demand?
These Optimas Resources Can Help
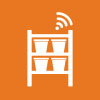
Do You Have Too Much Excess and Obsolete Inventory?
These Optimas Resources Can Help
The OptiTech VMI Cycle
From order through replenishment, Optimas’ tech-enabled inventory management solutions automate every aspect of the stocking process. OptiTech advanced VMI offerings use multiple, secure technologies to ensure fastener supply chain continuity. This Just-In-Time (JIT) system feeds demand-planning software that blends real-time consumption and market forecast data to optimize your inventory replenishment cycle.


Step 1:
Order TriggersStep 1
Part hits minimum trigger, OptiTech auto transmits a signal to create a replenishment order.

Step 2:
Package & ShipStep 2
Optimas picks, packs, labels and delivers to your specifications (dock, market, area racks, and/or point-of-use).

Step 3:
Audit & OptimizeStep 3
Optimas systematically audits for all quality categories (SKUs, quantities, labels, safety and accessibility) and optimizes to elevate efficiency.
Delivery Programs
1
DOCK TO DOCK
Stock is delivered to a single location.
2
DOCK TO SUPERMARKET
Stock is delivered to a designated area(s) close to the point of use.
3
DOCK TO LINE
Stock is delivered to the point of use.
Tech-Enabled Inventory Management Solutions
OptiTech solutions provides access to customized, real-time reports for greater transparency into your inventory and consumption data. Any OptiTech configuration works with a single- or multiple-bin Kanban system. Using EDI and web tools, OptiTech integrates into your ERP and legacy systems for easy processing of orders, shipping notifications and invoicing.
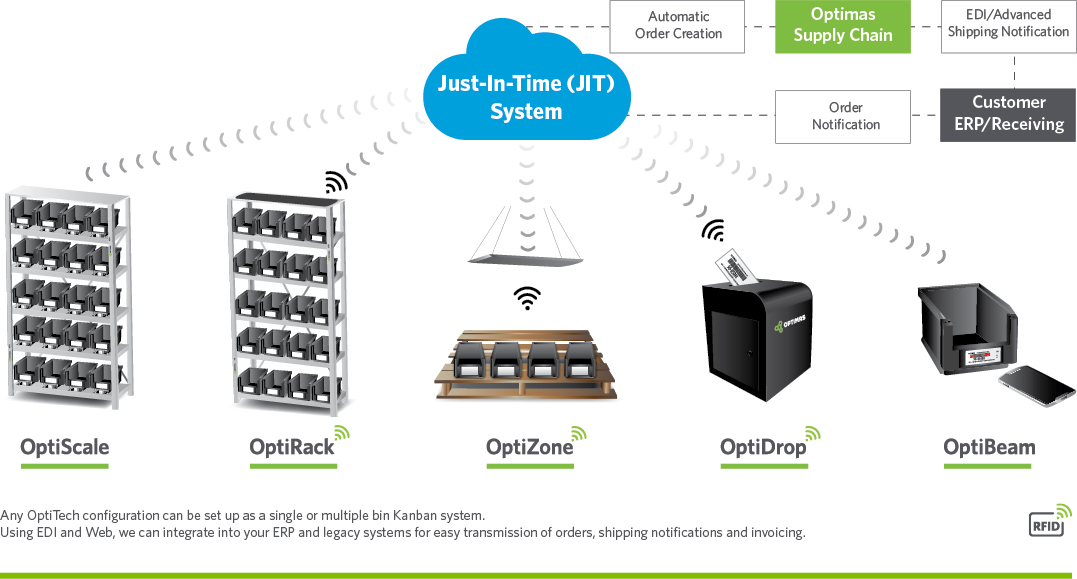
Click on our technologies for details.
Swipe left for technology details.
Inventory Management Solutions + Optimas Engineering
Application and manufacturing engineers, with decades of experience, design part functionality and optimize cold-form production. Industrial engineers identify wasteful practices inside customer facilities and devise more efficient production solutions.
Ensure You Have the Right Parts

Part Rationalization
Uncover ways to consolidate and standardize your SKUs to reduce cost and complexity.

Part Standardization
Develop a universal catalog of standard fastener parts for use across multiple programs.

Optimization
Identify and optimize the best process and tools for efficient production.
Ensure You Have the Right Process

Line Walks
Assess your operations for increased productivity, efficiency and labor savings.

Part Consolidation
Find alternative solutions and ways to re-engineer parts for design, cost and quality improvements.

BOM Analysis
Streamline your bill of materials and increase your speed to market.
Getting Started
Implementing an inventory management solution is the new monarch in industrial manufacturing. It’s essential to have a few things in place to ensure a smooth transition. Read our white paper to learn more about inventory management implementation best practices.
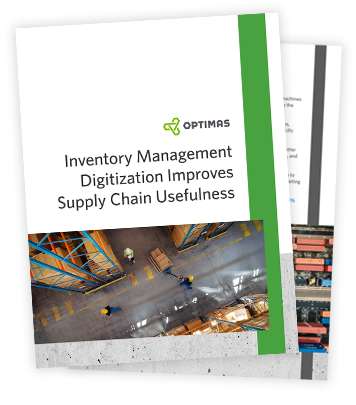
Real Results, Real Impact